2025 Autore: Howard Calhoun | [email protected]. Ultima modifica: 2025-01-24 13:19
Il capo di qualsiasi impresa, indipendentemente dal campo di attività, sogna che i profitti crescano e i costi di produzione rimangano invariati. Il sistema "5S" in produzione (nella versione inglese 5S), che si basa solo sull'uso razionale delle riserve interne, aiuta a raggiungere questo risultato.
Questo sistema non è stato creato da zero. Qualcosa di simile alla fine del XIX secolo fu proposto dall'americano Frederick Taylor. In Russia, lo ha fatto lo scienziato, rivoluzionario, filosofo e ideologo A. A. Bogdanov, che pubblicò un libro sui principi della gestione scientifica nel 1911. Sulla base delle disposizioni in essa contenute, l'URSS ha introdotto il NOT, cioè l'organizzazione scientifica del lavoro. Ma il più perfetto è stato il sistema 5C proposto dall'ingegnere giapponese Taiichi Ohno e da lui introdotto nello stabilimento Toyota Motor in produzione. Che cos'è e perché il sistema giapponese è diventato così popolare?
Il fatto è che si basa su un semplice principio che non richiede costi. Consiste inil prossimo: ogni dipendente, dall'addetto alle pulizie al direttore, dovrebbe ottimizzare il più possibile la sua parte nel flusso di lavoro generale. Ciò porta ad un aumento del profitto della produzione nel suo insieme e ad un aumento del reddito di tutti i suoi dipendenti. Ora il testimone dell'introduzione del sistema "5C" è stato raccolto da imprese di tutto il mondo, inclusa la Russia. In questo articolo cercheremo di convincere gli scettici che il know-how giapponese funziona davvero e in qualsiasi campo di attività.
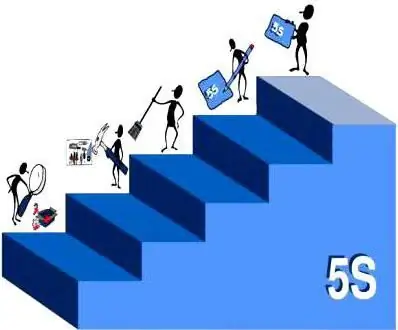
Il sistema "5C" in produzione, cos'è
International 5S sta per cinque passi ("step" in inglese step). Alcuni economisti e promotori di una nuova attitudine al lavoro spiegano il nome con i cinque postulati giapponesi che sono costantemente implementati nel sistema 5S: seiri, seiton, seiso, seiketsu e shitsuke. Per noi, le nostre "5C" native sono più vicine e comprensibili: cinque passaggi consecutivi che devono essere completati per raggiungere la prosperità della nostra produzione. Questo è:
1. Ordina.
2. Mantenere l'ordine.
3. Mantenersi puliti.
4. Standardizzazione.
5. Miglioramento.
Come puoi vedere, il sistema "5C" non richiede nulla di soprannaturale nella produzione. Forse è per questo che si può ancora incontrare sfiducia e un atteggiamento frivolo nei suoi confronti.
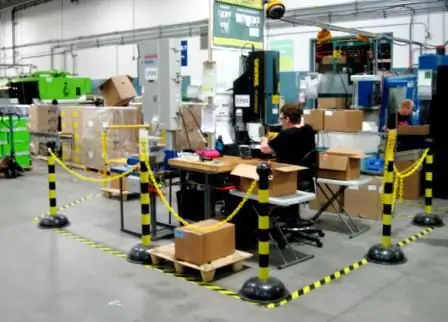
Fasi della creazione di un sistema
Il saggio giapponese Taiichi Ohno, che grazie all'introduzione dei suoi metodi nello stabilimento Toyota, riuscì a risollevarsiingegnere al CEO, ha notato quante perdite si verificano a causa di varie incoerenze e sovrapposizioni. Ad esempio, alcune piccole coclee non sono state posizionate in tempo sul nastro trasportatore e, di conseguenza, l'intera produzione si è interrotta. O viceversa, le parti sono state fornite con un margine, si sono rivelate superflue e, di conseguenza, uno dei dipendenti ha dovuto riportarle al magazzino, il che significa perdere tempo con il lavoro a vuoto. Taiichi Ohno ha sviluppato un concetto che ha chiamato "just in time". Cioè, ora sono state consegnate al nastro trasportatore esattamente tutte le parti necessarie.
Si potrebbero fare altri esempi. Il sistema "5S" in produzione includeva anche il concetto di "kanban", che in giapponese significa "segno pubblicitario". Taiichi Ohno ha suggerito di allegare un cosiddetto tag "kanban" a ciascuna parte oa ogni strumento, in cui sono state fornite tutte le informazioni necessarie sulla parte o sull'utensile. Fondamentalmente, si applica a qualsiasi cosa. Ad esempio, a merci, medicinali, cartelle in ufficio. Il terzo concetto su cui si basa il sistema 5S in produzione è il concetto di "kaizen", che significa miglioramento continuo. Sono stati concepiti anche altri concetti, adatti solo a processi produttivi altamente specializzati. In questo articolo, non li considereremo. Come risultato di tutte le innovazioni sperimentate nella pratica, si sono formati 5 step applicabili a qualsiasi produzione. Analizziamoli in dettaglio.
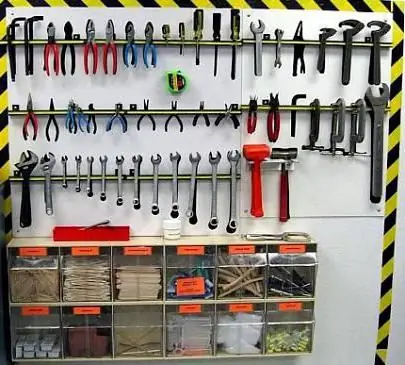
Ordinamento
Molti di noi hanno elementi sui nostri desktop che, infondamentalmente non necessario. Ad esempio, vecchi moduli, fascicoli inutilizzati, bozze di calcoli, un tovagliolo su cui c'era una tazza di caffè. E in questo caos potrebbero esserci i file oi documenti necessari. I principi di base del sistema "5S" riguardano l'ottimizzazione del flusso di lavoro, ovvero fare in modo che non si perda tempo a cercare le cose giuste tra le macerie del superfluo. Questo è l'ordinamento. Cioè, sul posto di lavoro (vicino alla macchina, sul tavolo, in officina - ovunque), tutti gli articoli sono disposti in due pile: il necessario e il non necessario, che devono essere sm altiti. Inoltre, tutto ciò di cui hai bisogno viene scomposto nelle seguenti pile: "usato spesso e costantemente", "usato raramente", "quasi non usato". Questo completa l'ordinamento.
Mantenimento dell'ordine
Se smonti semplicemente gli oggetti, non avrà senso. È necessario disporre questi elementi (strumenti, documenti) in modo tale che ciò che viene utilizzato costantemente e spesso sia in vista, o in modo che possa essere rapidamente preso e riposto facilmente. Ciò che viene utilizzato raramente può essere inviato da qualche parte in una scatola, ma è necessario allegare un tag kanban in modo che dopo un po' possa essere trovato facilmente e con precisione. Come puoi vedere, il sistema 5S sul posto di lavoro parte dai passaggi più semplici, ma in re altà si rivela molto efficace. Inoltre, migliora l'umore e il desiderio di lavorare.
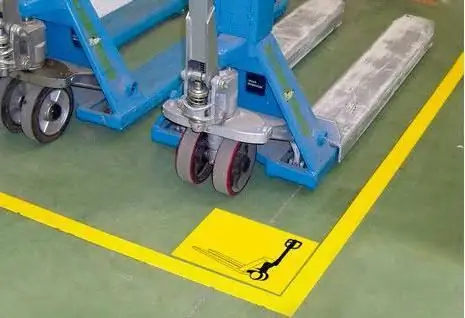
Mantenersi puliti
Questo terzo passo è il più logico per molti. Ci viene insegnato ad essere puliti fin dall'infanzia. Sulin produzione, è anche necessario, e non solo i tavoli degli impiegati o gli armadi negli esercizi di ristorazione, ma anche le macchine, i locali di servizio degli addetti alle pulizie dovrebbero essere puliti. In Giappone, i dipendenti si prendono cura dei loro luoghi di lavoro, vengono puliti tre volte al giorno: la mattina prima del lavoro, all'ora di pranzo e la sera, alla fine della giornata lavorativa. Inoltre, le loro imprese hanno introdotto una marcatura speciale delle aree che consentono loro di osservare l'ordine nella produzione, ovvero le aree dei prodotti finiti, lo stoccaggio di alcune parti e così via sono contrassegnate con colori diversi.
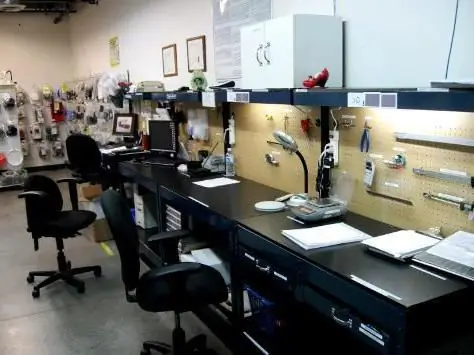
Standardizzazione
I principi di standardizzazione sono stati inventati da Taiichi Ohno. Sono anche ampiamente utilizzati dal moderno sistema 5S. La gestione della produzione, grazie alla standardizzazione, riceve uno strumento meraviglioso per il controllo di tutti i processi. Di conseguenza, le cause dei ritardi rispetto al programma vengono rapidamente eliminate e vengono corretti gli errori che portano al rilascio di prodotti di bassa qualità. Nello stabilimento Toyota Motor, la standardizzazione si presentava così: i capisquadra elaboravano piani di lavoro giornalieri, venivano affisse istruzioni precise sul posto di lavoro e, alla fine della giornata lavorativa, operai speciali verificavano quali deviazioni dal piano si verificavano durante la giornata e perché. Questa è la regola base della standardizzazione, ovvero istruzioni precise, piani di lavoro e controllo sulla loro attuazione. Ora molte imprese, ad esempio gli stabilimenti ENSTO in Estonia, stanno introducendo un sistema di bonus per i dipendenti che rispettano rigorosamente le disposizioni del sistema 5C e, sulla base di ciò, aumentano la loro produttività, cheè un grande incentivo ad adottare questo sistema come stile di vita.
Miglioramento
Il quinto passaggio, che completa il sistema "5S" in produzione, si basa sul concetto di kaizen. Significa che tutti i dipendenti, indipendentemente dalla loro posizione, dovrebbero adoperarsi per migliorare il processo di lavoro nell'area a loro affidata. L'essenza filosofica del kaizen è che tutta la nostra vita migliora ogni giorno, e poiché il lavoro fa parte della vita, non dovrebbe nemmeno rimanere lontano dai miglioramenti.
Il campo di attività qui è ampio, perché la perfezione non ha limiti. Secondo i concetti dei giapponesi, gli stessi lavoratori dovrebbero voler migliorare il loro processo produttivo, senza istruzioni o coercizioni. Ora molte organizzazioni stanno creando team di lavoratori che monitorano la qualità dei prodotti, insegnano la loro esperienza positiva agli altri e aiutano a raggiungere l'eccellenza.
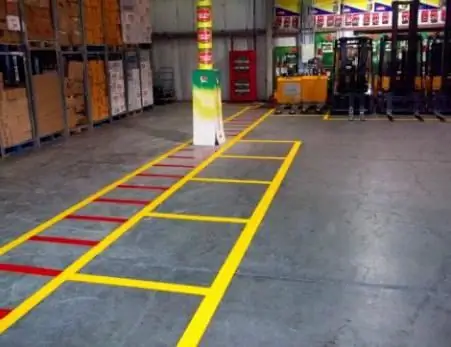
Errori di base
Affinché il sistema "5C" inizi a funzionare, non è sufficiente organizzarlo o assumere dipendenti che costringeranno i colleghi a implementarlo. È importante che le persone si rendano conto dell'utilità di questa innovazione e la accettino come uno stile di vita. L'introduzione del sistema "5S" in Russia in produzione incontra delle difficoltà proprio perché la nostra mentalità russa è diversa da quella giapponese. Molte delle nostre produzioni sono caratterizzate da:
1. I dipendenti, soprattutto se non ci sono incentivi per loro, non cercano di aumentare i profitti dell'impresa. Stanno chiedendo,perché cercare di rendere il capo ancora più ricco se ha già tutto.
2. I leader stessi non sono interessati all'introduzione del sistema "5S", perché non ne vedono l'opportunità.
3. Molte direttive "dal basso dall' alto" sono solite eseguire solo per "tick". In Giappone, c'è un atteggiamento completamente diverso nei confronti del loro lavoro. Ad esempio, lo stesso Taiichi Ohno, introducendo il sistema "5S", non pensava al guadagno personale, ma al vantaggio dell'azienda in cui era solo un ingegnere.
4. In molte aziende, il sistema 5S viene introdotto forzatamente. La produzione snella, che implica l'eliminazione di perdite di ogni tipo (orario di lavoro, materie prime, buoni dipendenti, motivazione e altri indicatori), non funziona, poiché i lavoratori iniziano a resistere alle innovazioni a livello inconscio, il che alla fine riduce a zero tutti gli sforzi.
5. I manager che implementano il sistema non ne comprendono appieno l'essenza, il che causa guasti nei processi di produzione stabiliti.
6. La standardizzazione spesso si trasforma in burocrazia, una buona azione è invasa da istruzioni e direttive che interferiscono solo con il lavoro.
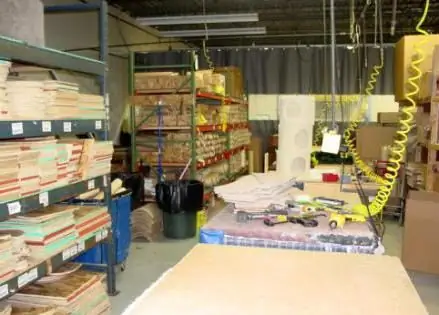
Recensioni
Russi che hanno introdotto in produzione il sistema "5S", il feedback su questa innovazione è molto ambiguo. Pro evidenziati:
- meglio essere sul posto di lavoro;
- non distrarre dal lavoro con piccole cose inutili;
- flusso di lavoro più chiaro;
- fatica diminuita alla fine del turno;
- leggermente aumentatostipendio aumentando la produttività del lavoro;
- infortuni sul lavoro diminuiti.
Contro noti:
- durante lo smistamento, costringono tutto a essere buttato via;
- la standardizzazione ha portato ad un aumento della burocrazia;
- L'introduzione del sistema "5C" non ha esacerbato i problemi in tutte le aree dell'impresa;
- Mettere il sistema 5S al primo posto ha messo in ombra questioni importanti come la mancanza di pezzi di ricambio.
Consigliato:
Sistema "Rapida": descrizione, caratteristiche e recensioni
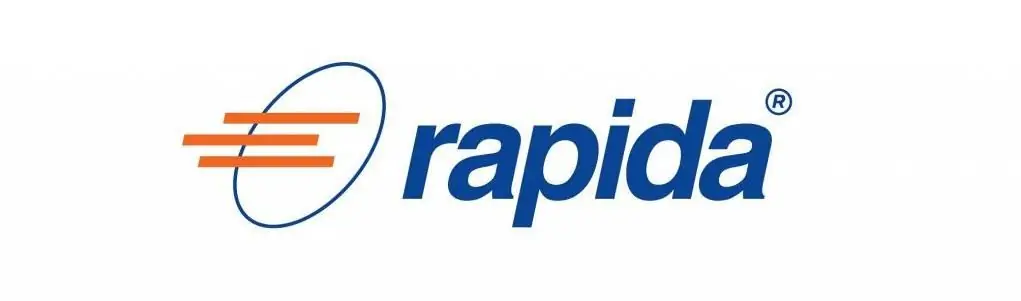
Il sistema di pagamento "Rapida" è un servizio universale. I suoi servizi sono adatti sia per utenti ordinari che per imprenditori. Considera le caratteristiche della piattaforma e come si svolge la procedura di registrazione e identificazione dei clienti
Produzione moderna. La struttura della produzione moderna. Problemi della produzione moderna

L'industria sviluppata e un alto livello dell'economia del paese sono fattori chiave che influenzano la ricchezza e il benessere della sua gente. Un tale stato ha grandi opportunità e potenzialità economiche. Una componente significativa dell'economia di molti paesi è la produzione
Produzione di gas. Metodi di produzione del gas. Produzione di gas in Russia
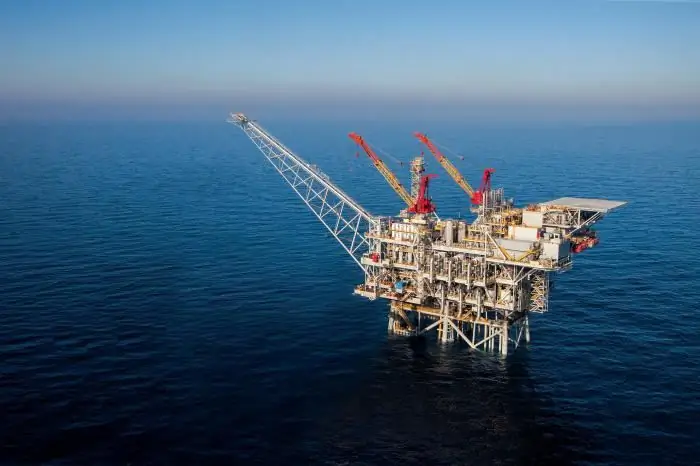
Il gas naturale si forma mescolando vari gas nella crosta terrestre. Nella maggior parte dei casi, la profondità di occorrenza varia da diverse centinaia di metri a un paio di chilometri. Vale la pena notare che il gas può formarsi a temperature e pressioni elevate. In questo caso, non c'è accesso di ossigeno al luogo. Ad oggi, la produzione di gas è stata implementata in diversi modi, ognuno dei quali considereremo in questo articolo. Ma parliamo di tutto in ordine
Pomodoro "Lady's man": recensioni, descrizione, caratteristiche, caratteristiche della coltivazione
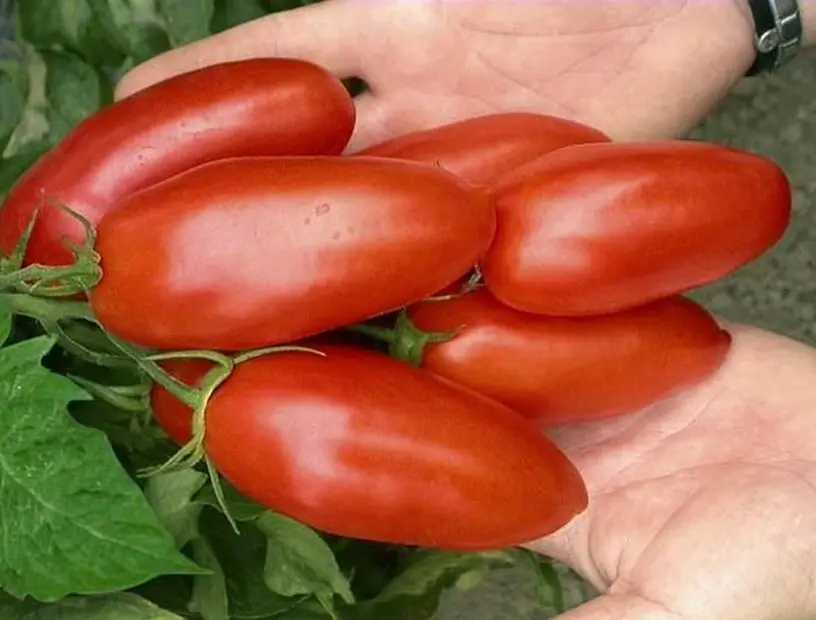
Oggi, la varietà di pomodoro "Lady's Man", le cui recensioni sono estremamente positive, è leader tra i pomodori a maturazione precoce. I giardinieri dilettanti che hanno piantato almeno una volta nei loro letti sono sempre rimasti dei fan"
"Kanban", sistema di produzione: descrizione, essenza, funzioni e recensioni
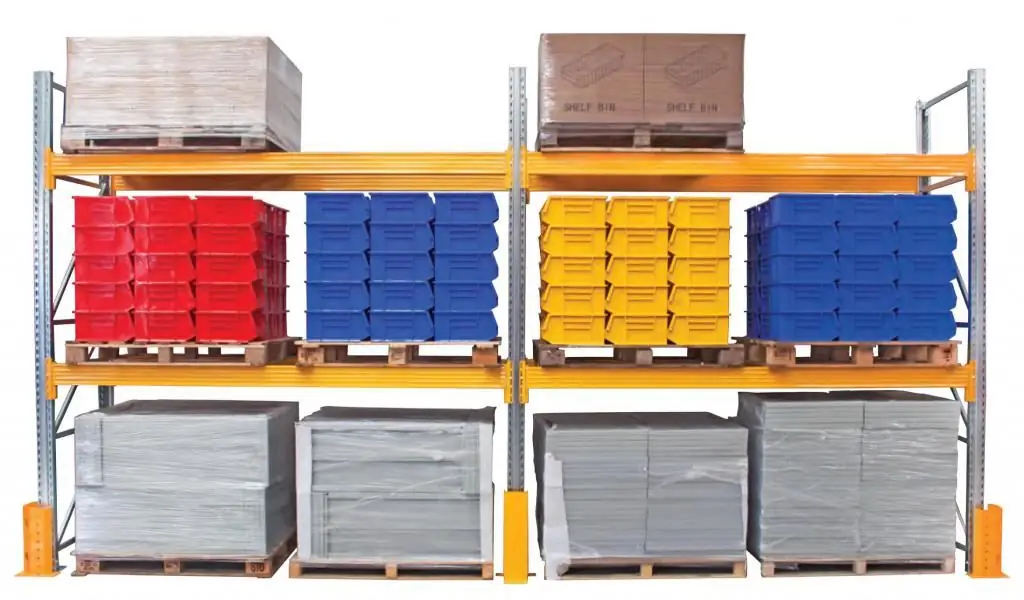
Kanban è il metodo di gestione della produzione industriale più noto all'interno del concetto Just-in-Time. Con costi di organizzazione minimi, può ridurre significativamente il tempo di lavoro e il costo delle risorse materiali