2025 Autore: Howard Calhoun | [email protected]. Ultima modifica: 2025-01-24 13:18
Le scorie granulari d' altoforno sono uno spreco della produzione metallurgica. Per essere più precisi, questa è la materia prima che rimane dopo la fusione della ghisa negli altiforni.
Cos'è la scoria e da dove viene?
Per produrre materie prime come la ghisa, alcune materie prime devono essere caricate nell' altoforno. Tali materiali erano minerale di ferro, pietra di flusso, coke. All'uscita dalla fornace si ottengono solo due sostanze: ghisa e scorie. La composizione delle scorie di altoforno comprende sostanze come quarzo, ossidi di alluminio (lavorazione dal minerale di ferro), ossidi di calcio e magnesio (rifiuti di pietre di flusso). La scoria fusa ottenuta all'uscita dell' altoforno può avere una temperatura di 1500 gradi Celsius, e in alcuni casi anche di più. Naturalmente è necessario il raffreddamento del materiale. Attualmente gli impianti utilizzano solo 4 tipi principali di lavorazione delle scorie da altoforno.
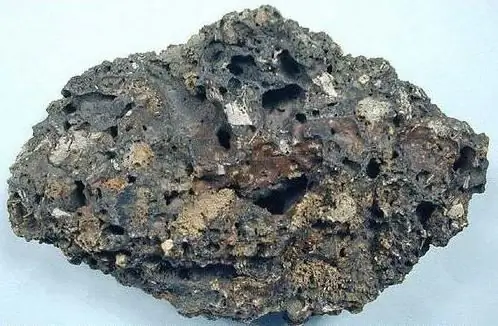
- Il primo metodo prevede il raffreddamento della materia prima con normale acqua fredda. Questa operazione è anche chiamata rigonfiamento delle scorie.
- Il secondo metodo utilizza il raffreddamentosostanze con l'aiuto dell'aria.
- Il terzo modo è schiacciante.
- Quarto - macinazione.
Componenti materiali principali e risultati di lavorazione
È importante qui notare che la scelta del metodo di lavorazione delle scorie d' altoforno determinerà quale tipo di sostanza si otterrà alla fine e quali proprietà avrà. Ogni metodo conferisce qualità uniche alla materia prima. Un' altra importante osservazione è che i principali ossidi che fanno parte delle scorie - ossidi di magnesio, calcio e alluminio, non si trovano in natura in forma libera. In altre parole, non esistono e possono essere ottenuti solo dalla lavorazione di scorie e minerali di ferro in un altoforno. Oltre ai principali ossidi, la composizione della sostanza comprende manganese, composti di ferro e zolfo, quarzo.
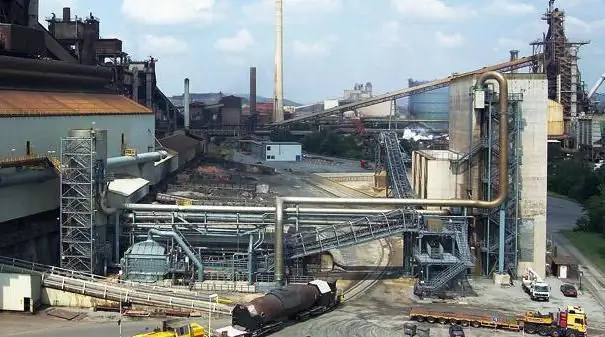
Ad esempio, se si ricorre al raffreddamento del materiale esausto con aria, la composizione delle scorie d' altoforno sarà approssimativamente la seguente: silicati e materiali alluminosilicati come wolastonite, melilite e merwinite.
Com'è il processo di granulazione?
Il processo di granulazione di una sostanza viene effettuato mediante il metodo del raffreddamento rapido delle materie prime fuse. È importante qui aggiungere che in alcuni casi può essere aggiunto un processo di frantumazione meccanica, scoria ancora liquida o già semisolidata. Lo scopo principale di questa operazione è trasformare grandi pezzi di materiale in grani più piccoli che saranno più convenienti da lavorare in futuro, nonché migliorare la qualità dell'attività idraulica. essoun'operazione molto importante, poiché questa proprietà è la più importante, poiché le scorie possono essere utilizzate come componente costituente dei cementi di scoria e possono anche fungere da additivo per il cemento Portland.
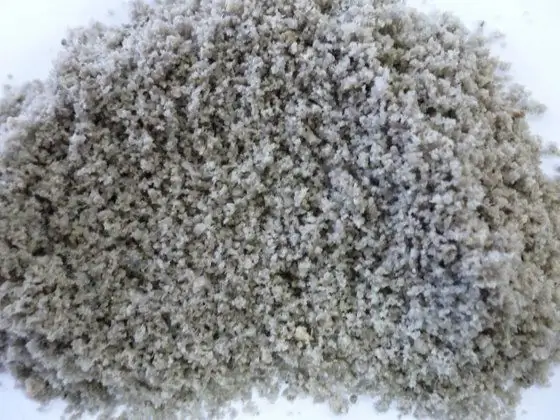
Devi capire che non esiste una produzione speciale di scorie di altoforno in quanto tali. Si ottiene solo elaborando minerali e altre sostanze in un altoforno.
Metodi di granulazione
Devi sapere che per la granulazione degli scarti di produzione, cioè le scorie, esistono diversi metodi, oltre ai dispositivi che effettuano questa operazione. A seconda del contenuto di umidità delle scorie alla fine, le installazioni sono suddivise in tipi. Ci sono unità per la granulazione a umido e semisecco.

Se viene eseguito il metodo di granulazione a umido, le scorie caricate nei secchi per scorie in forma calda vengono alimentate in bacini di cemento armato riempiti d'acqua. Successivamente, dai mestoli si fonde in queste vasche attraverso apposite grondaie. Un leggero vantaggio del metodo è che le piscine sono divise in più sezioni. Ciò consente di eseguire il processo di raffreddamento in modo quasi continuo. Quando la sostanza rovente si fonde in una sezione, le scorie d' altoforno già raffreddate possono essere scaricate contemporaneamente dall' altra. Per la spedizione delle materie prime, gli stabilimenti dispongono di gru a conchiglia che la consegnano direttamente a vagoni ferroviari di tipo aperto. Successivamente, le scorie vengono consegnate al magazzino o direttamente al consumatore.
Contenutoumidità
Vale la pena notare qui che il contenuto di umidità del materiale dipende dal peso totale delle scorie dell' altoforno che subiscono il processo di granulazione. In altre parole, più la struttura dei grani è porosa, più umidità rimane al loro interno. La formazione di pori nella scoria granulare solidificata si verifica a causa dell'azione dei gas. Queste sostanze volatili sono contenute nella materia prima fusa e iniziano ad evaporare quando la temperatura della scoria diminuisce, cioè quando viene raffreddata. Tuttavia, è importante notare qui che il raffreddamento e la solidificazione del materiale avvengono così rapidamente che il gas non ha il tempo di evaporare dalle scorie. Rimane all'interno sotto forma di piccole bolle, che creano la struttura porosa dei grani. Porosità e, per questo motivo, anche il contenuto di umidità delle scorie dipende direttamente dalle condizioni utilizzate direttamente nel processo di raffreddamento delle scorie. Cioè, non solo il risultato finale, ma anche la struttura stessa dipende dalla scelta del metodo.
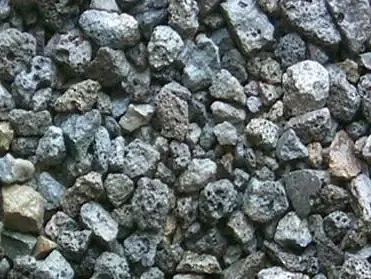
Metodo semisecco
La scoria semisecca si ottiene utilizzando il metodo della frantumazione meccanica, oltre che gettando in aria scorie pre-raffreddate, ma allo stesso tempo non ancora solidificate. Pertanto, la struttura del materiale risulta essere molto più densa, il che aumenta notevolmente il peso fisico di circa una volta e mezza, rispetto al peso che avrebbe la scoria se passasse per granulazione a umido, avendo la stessa quantità iniziale di sostanza. Se parliamo di una caratteristica come l'umidità, per le materie prime umide questo valore è compreso tra il 15 e il 35%, abbastanzararamente il 10%. Mentre la granulazione a secco è accompagnata da un'umidità delle scorie che varia dal 5 al 10%. Se confrontiamo il peso volumetrico, con un metodo di lavorazione a umido sarà compreso tra 400 e 1000 kg / m e con uno secco - tra 600 e 1300 kg / m. Qui vale la pena aggiungere che con l'aumento della temperatura di fusione in altoforno, il peso finale delle scorie di altoforno diminuirà.
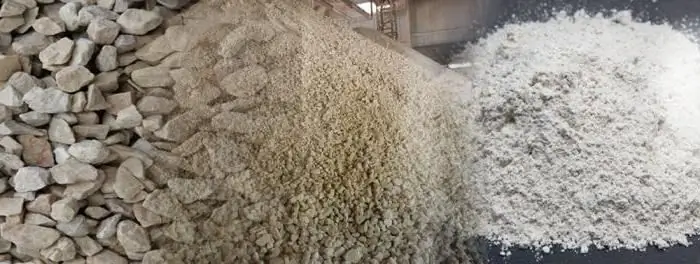
È importante aggiungere che la maggior parte degli stabilimenti utilizza la granulazione a umido, nonostante il metodo presenti diversi svantaggi:
- Elevato consumo di carburante per asciugare il materiale prima che si rompa.
- La produttività delle apparecchiature per l'essiccazione delle scorie è bassa.
- Congelamento delle scorie bagnate in carri, magazzini e altre aree di stoccaggio in inverno.
Scoria d' altoforno GOST 3476-74
Questo standard descrive tutti i requisiti tecnici, i metodi di prova e le regole di accettazione, nonché i metodi per lo stoccaggio e il trasporto delle scorie di altoforno. Uno dei punti del documento statale riguarda il contenuto di umidità delle materie prime. Si dice che la percentuale di umidità deve corrispondere a quella concordata tra cliente e fornitore. In altre parole, si può dire che il cliente sceglie il metodo di granulazione del materiale.
Consigliato:
Produzione moderna. La struttura della produzione moderna. Problemi della produzione moderna

L'industria sviluppata e un alto livello dell'economia del paese sono fattori chiave che influenzano la ricchezza e il benessere della sua gente. Un tale stato ha grandi opportunità e potenzialità economiche. Una componente significativa dell'economia di molti paesi è la produzione
Il bronzo è una composizione in lega. La composizione chimica del bronzo
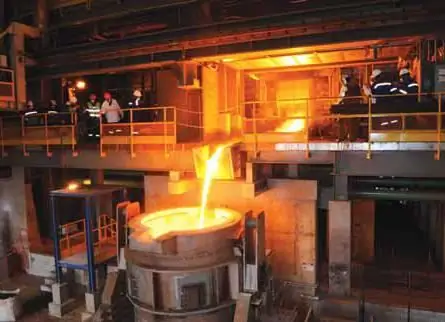
Molte persone sanno del bronzo solo che da esso vengono fuse sculture e monumenti. In effetti, questo metallo è immeritatamente privato dell'attenzione popolare. Dopotutto, non è stato un vano che nella storia dell'umanità ci sia stata persino un'età del bronzo, un'intera epoca durante la quale la lega ha occupato una posizione dominante. Le qualità possedute da una lega di rame e stagno sono semplicemente indispensabili in molte industrie. Viene utilizzato nella fabbricazione di strumenti, nell'ingegneria meccanica, nella fusione delle campane delle chiese e così via
Produzione di gas. Metodi di produzione del gas. Produzione di gas in Russia
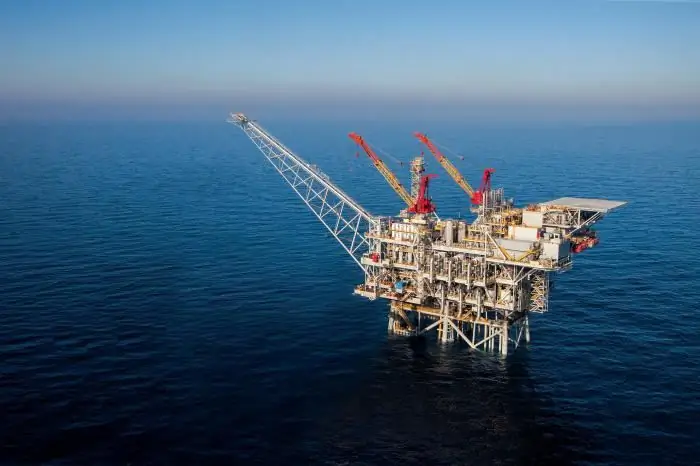
Il gas naturale si forma mescolando vari gas nella crosta terrestre. Nella maggior parte dei casi, la profondità di occorrenza varia da diverse centinaia di metri a un paio di chilometri. Vale la pena notare che il gas può formarsi a temperature e pressioni elevate. In questo caso, non c'è accesso di ossigeno al luogo. Ad oggi, la produzione di gas è stata implementata in diversi modi, ognuno dei quali considereremo in questo articolo. Ma parliamo di tutto in ordine
Composizione di sapone per la produzione domestica. Idea imprenditoriale
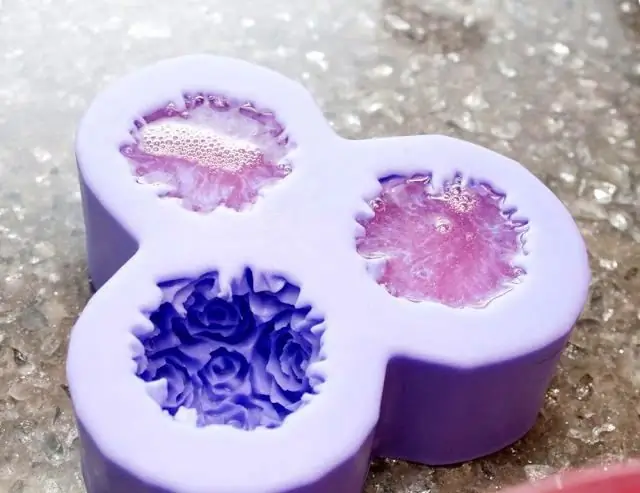
La produzione di sapone per la casa, come dimostra la pratica, è un'attività molto redditizia. La composizione di questo prodotto può essere qualsiasi cosa, dalle opzioni economiche a quelle d'élite. L'indubbio vantaggio della produzione di sapone sono i bassi costi necessari per avviare un'impresa. Il periodo di ammortamento per un tale progetto sarà di circa sei mesi. La redditività è compresa tra il 40 e il 50 percento. Allettante? Allora questo articolo è per te
Acciaio: composizione, proprietà, tipologie e applicazioni. Composizione di acciaio inossidabile
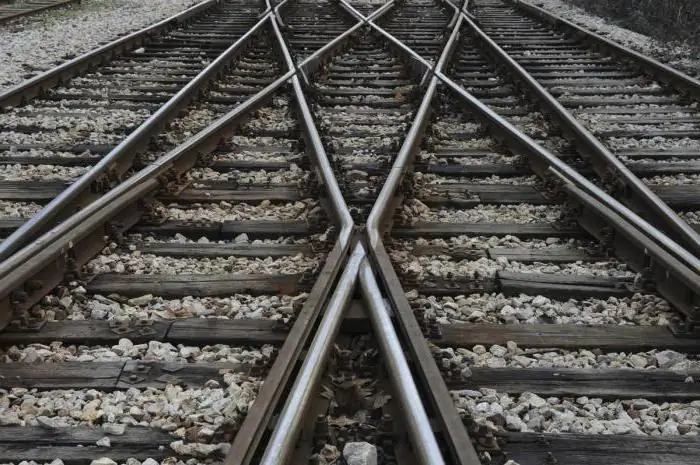
Oggi l'acciaio è utilizzato nella stragrande maggioranza delle industrie. Non tutti però sanno che la composizione dell'acciaio, le sue proprietà, tipologie e applicazioni sono molto diverse dal processo produttivo di questo prodotto