2025 Autore: Howard Calhoun | [email protected]. Ultima modifica: 2025-01-24 13:18
Un forno ad arco in acciaio (EAF) è un dispositivo che riscalda il materiale mediante piegatura elettrica.
Gli apparecchi industriali variano in dimensioni da piccole unità, circa una tonnellata di potenza (utilizzata nelle fonderie per realizzare prodotti in ghisa) a 400 unità per tonnellata, utilizzate per il riciclaggio dell'acciaio. I forni per acciaio ad arco, EAF, utilizzati nei laboratori di ricerca possono avere una capacità di poche decine di grammi. La temperatura dei dispositivi industriali può raggiungere i 1800 °C (3272 °F), mentre le installazioni di laboratorio superano i 3000 °C (5432 °F).
I forni per acciaio ad arco (EAF) differiscono dai forni a induzione in quanto il materiale caricato è direttamente soggetto a flessione elettrica e la corrente ai terminali passa attraverso il materiale caricato.
Costruzione
Il forno per acciaio ad arco viene utilizzato per la produzione di acciaio ed è composto da un recipiente in refrattario. Principalmente diviso in tre sezioni:
- Shell, composto da pareti laterali e fondo in acciaiociotole.
- Pallet di materiale refrattario.
- Tetto. Può essere con rivestimento resistente al calore o raffreddato ad acqua. Ed è anche realizzato a forma di palla o tronco di cono (sezione conica). Il tetto supporta anche un delta refrattario al centro attraverso il quale entrano uno o più elettrodi di grafite.
Singoli oggetti
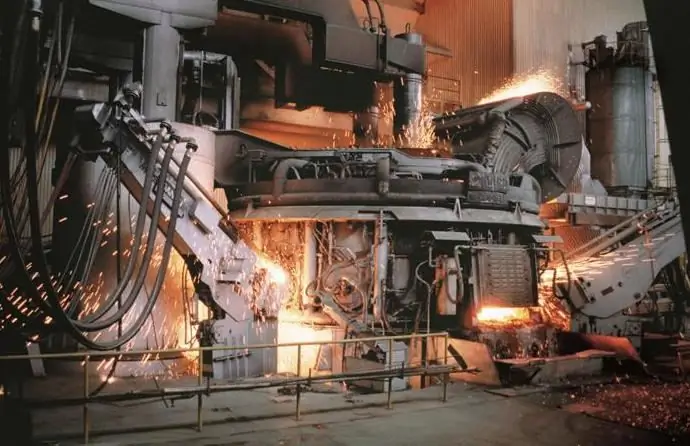
Il focolare può avere una forma semisferica ed è necessario in un forno eccentrico per picchiettare il fondo. Nelle officine moderne, la fornace per acciaio ad arco - EAF 5 - è spesso sopraelevata rispetto al piano terra in modo da poter manovrare facilmente mestoli e recipienti per scorie sotto le due estremità. Separati dalla struttura si trovano il supporto degli elettrodi e l'impianto elettrico, nonché la piattaforma inclinata su cui poggia lo strumento.
Strumento unico
Un tipico forno ad arco per la fusione dell'acciaio EAF 3 è alimentato da una sorgente trifase e quindi ha tre elettrodi. Hanno sezione tonda e, di norma, segmenti con attacchi filettati, in modo che man mano che si usurano si possano aggiungere nuovi elementi.
L'arco si forma tra il materiale caricato e l'elettrodo. La carica viene riscaldata sia dalla corrente che la attraversa sia dall'energia irradiata rilasciata dall'onda. La temperatura raggiunge circa 3000 °C (5000 °F), facendo brillare le sezioni inferiori degli elettrodi come lampade a incandescenza quando il forno ad arco è in funzione.
Gli elementi vengono alzati e abbassati automaticamente da un sistema di posizionamento che può utilizzare qualsiasi elettricoverricello, argani o cilindri idraulici. La regolazione mantiene una corrente pressoché costante. Qual è il consumo di energia di un forno ad arco? Viene mantenuto costante durante la fusione della carica, anche se lo sfrido può spostarsi sotto gli elettrodi mentre si scioglie. I manicotti dell'albero che tengono l'elemento possono trasportare sbarre pesanti (che possono essere tubi di rame cavi raffreddati ad acqua che forniscono corrente ai morsetti) o "maniche calde" dove l'intera parte superiore trasporta la carica, aumentando l'efficienza.
Quest'ultimo tipo può essere realizzato in acciaio ramato o in alluminio. Cavi di grandi dimensioni raffreddati ad acqua collegano sbarre o staffe a un trasformatore posizionato accanto al forno. Uno strumento simile viene installato in magazzino e raffreddato con acqua.
Toccatura e altre operazioni
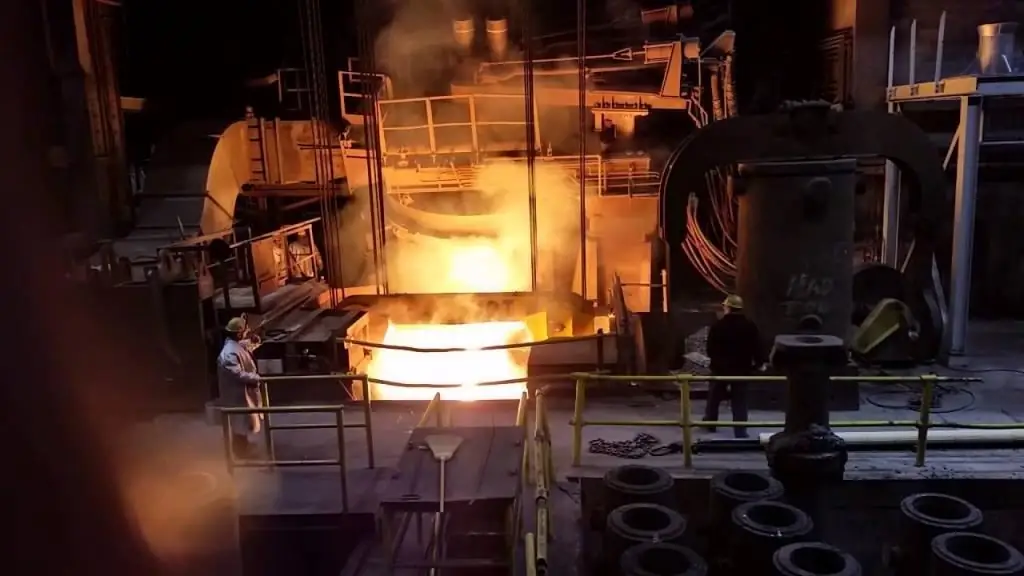
Il forno ad arco in acciaio EAF 50 è costruito su una piattaforma inclinata in modo che l'acciaio liquido possa essere versato in un altro contenitore per il trasporto. L'operazione di rib altamento per trasferire l'acciaio fuso è chiamata maschiatura. Inizialmente, tutte le volte di fabbricazione dell'acciaio del forno ad arco avevano uno scivolo di scarico ricoperto di refrattario, che veniva lavato via quando veniva inclinato.
Ma spesso le apparecchiature moderne hanno una valvola eccentrica di uscita inferiore (EBT) per ridurre l'incorporazione di azoto e scorie nell'acciaio liquido. Questi forni hanno un'apertura che scorre verticalmente attraverso il focolare e il guscio ed è decentrata in una stretta "bocca" a forma di uovo. È pienosabbia refrattaria.
Le piante moderne possono avere due gusci con un set di elettrodi che vengono fatti passare tra loro. La prima parte riscalda il rottame, mentre l' altra viene utilizzata per la fusione. Altri forni CC hanno un layout simile ma hanno elettrodi per ciascuna guaina e un set di componenti elettronici.
Elementi ossigeno
I forni a corrente alternata di solito hanno uno schema di punti caldi e freddi lungo il perimetro del focolare, situati tra gli elettrodi. In quelli moderni, i bruciatori a ossitaglio sono installati nella parete laterale. Sono utilizzati per fornire energia chimica alle zone negative, il che rende il riscaldamento dell'acciaio più uniforme. Ulteriore potenza viene fornita fornendo ossigeno e carbonio al forno. Storicamente questo veniva fatto con lance (tubi cavi in acciaio dolce) nella porta delle scorie, ora è principalmente fatto con unità di iniezione montate a parete che combinano bruciatori a ossitaglio e sistemi di alimentazione dell'aria in un'unica nave.
Un moderno forno per acciaio di medie dimensioni ha un trasformatore valutato a circa 60.000.000 di volt-amp (60 MVA), con una tensione secondaria da 400 a 900 e una corrente superiore a 44.000. In un negozio moderno, un tale si prevede che la fornace produrrà 80 tonnellate di acciaio liquido in circa 50 minuti dal caricamento dei rottami freddi alla maschiatura.
In confronto, i forni ad ossigeno di base possono avere una capacità di 150-300 tonnellate per lotto o "riscaldarsi" e generare calore per 30-40 minuti. Ci sono enormi differenze nei dettagli della progettazione e del funzionamento del forno,a seconda del prodotto finale e delle condizioni locali, oltre alla continua ricerca per migliorare l'efficienza dell'impianto.
Il più grande rottame solo (in termini di peso del rubinetto e potenza del trasformatore) è un dispositivo CC esportato dal Giappone con un peso del rubinetto di 420 tonnellate e alimentato da otto trasformatori da 32 MVA per una potenza totale di 256 MBA.
Ci vogliono circa 400 kilowattora per produrre una tonnellata di acciaio in un forno elettrico ad arco, o circa 440 kWh per metro. L'energia minima teorica richiesta per fondere rottami di acciaio è 300 kWh (punto di fusione 1520 °C / 2768 °F). Pertanto, un EAF da 300 tonnellate con una potenza di 300 MVA richiederà circa 132 MWh di energia e il tempo di accensione è di circa 37 minuti.
La produzione di acciaio utilizzando un arco elettrico è economicamente sostenibile solo se c'è abbastanza elettricità con una rete ben sviluppata. In molti luoghi i mulini funzionano durante le ore non di punta, quando i servizi pubblici hanno una capacità di produzione in eccesso e il prezzo al metro è inferiore.
Operazione
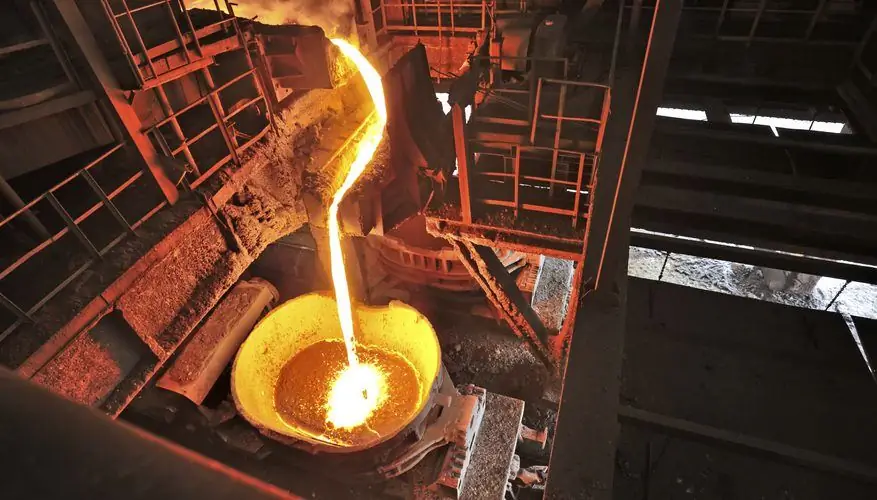
La fornace d'acciaio ad arco versa l'acciaio in una piccola siviera. I rottami metallici vengono consegnati in una rientranza situata accanto alla fonderia. I rottami tendono a presentarsi in due varietà principali: rottami (elettrodomestici, automobili e altri articoli similiacciaio leggero) e heavy melt (grandi lastre e travi), oltre a ferro ridotto diretto (DRI) o ghisa per l'equilibrio chimico. I forni separati fondono quasi il 100% DRI.
Fase successiva
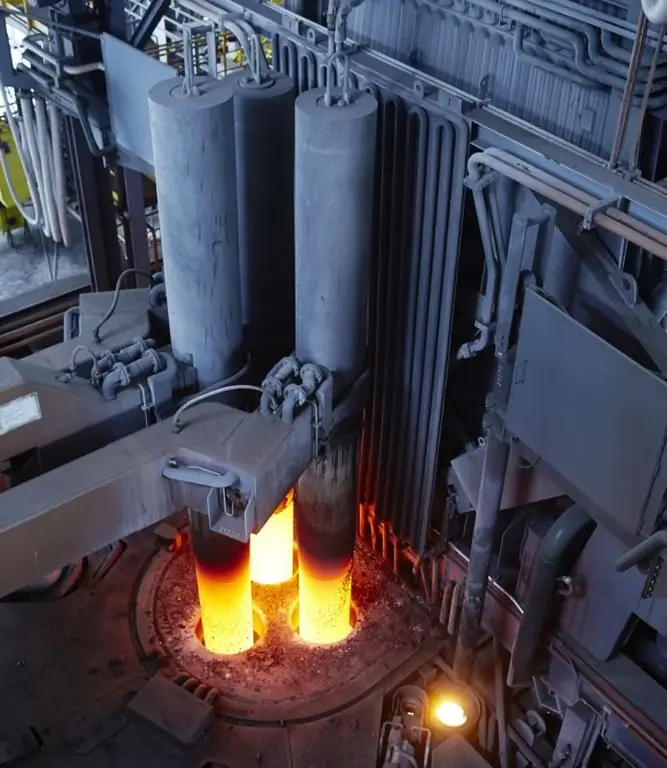
Lo scarto viene caricato in grandi secchi, chiamati cestini, con porte a conchiglia per la base. È necessario prestare attenzione per garantire che lo sfrido sia nel cestello per garantire il buon funzionamento del forno. Una forte fusione viene posata sopra con un leggero strato di un brandello protettivo, sopra il quale giace un' altra parte. Tutti devono essere presenti nel forno dopo il caricamento. A questo punto, il cestello può spostarsi nel preriscaldatore rottami, che utilizza i gas di scarico caldi della fonderia per recuperare energia, migliorando l'efficienza.
Overflow
Poi la nave viene portata alla fonderia, il tetto della fornace viene aperto e il materiale viene caricato al suo interno. Il trasferimento è una delle operazioni più pericolose per gli operatori. Molta energia potenziale viene rilasciata da tonnellate di metallo in caduta. Qualsiasi sostanza liquida nella fornace viene spesso spinta verso l' alto e verso l'esterno da rottami solidi e grasso. La polvere sul metallo si accende se il forno è caldo, provocando l'esplosione di una palla di fuoco.
In alcuni dispositivi a doppio guscio, lo sfrido viene caricato nel secondo mentre il primo si sta sciogliendo e viene preriscaldato dai gas di scarico della parte attiva. Altre operazioni sono: carico continuo e lavorazione a temperatura su nastro trasportatore, che poi scarica il metallo nel forno stesso. È possibile avviare altri dispositivisostanza calda da altre operazioni.
Tensione
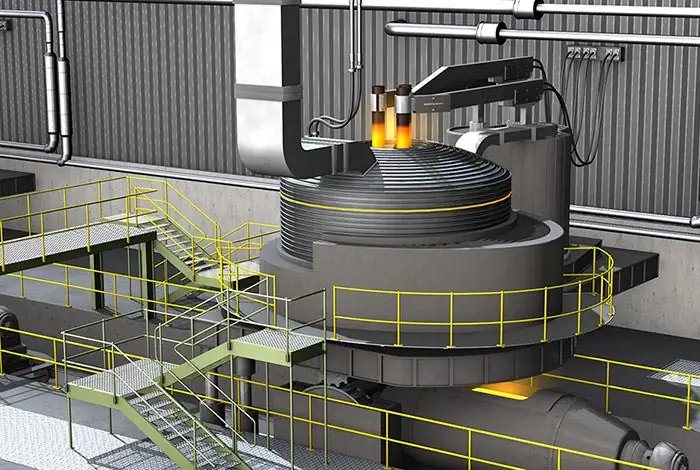
Dopo la carica, il tetto si appoggia all'indietro sul forno e inizia la fusione. Gli elettrodi vengono abbassati sul rottame metallico, viene creato un arco e quindi vengono posizionati in modo che si diffondano nello strato di briciole nella parte superiore del dispositivo. Per questa operazione vengono selezionate basse tensioni per proteggere il tetto e le pareti dal calore eccessivo e dai danni dell'arco.
Una volta che gli elettrodi hanno raggiunto la massa fusa alla base del forno e le onde sono schermate dal piede di porco, la tensione può essere aumentata e gli elettrodi leggermente sollevati, allungando e aumentando la potenza per la massa fusa. Ciò consente alla piscina fusa di formarsi più rapidamente, riducendo il tempo di prelievo.
L'ossigeno viene soffiato nei rottami metallici, bruciando o tagliando l'acciaio e il calore chimico aggiuntivo viene fornito dai bruciatori a parete. Entrambi i processi accelerano la fusione della sostanza. Gli ugelli supersonici consentono ai getti di ossigeno di penetrare nelle scorie schiumose e raggiungere il bagno liquido.
Ossidazione delle impurità
Una parte importante della produzione dell'acciaio è la formazione di scorie che galleggiano sulla superficie dell'acciaio fuso. Di solito è composto da ossidi metallici e funge anche da luogo per raccogliere le impurità ossidate, come una coperta termica (fermando l'eccessiva perdita di calore) e aiuta anche a ridurre l'erosione del rivestimento refrattario.
Per un forno con refrattari basici che producono acciaio al carbonio, i comuni formatori di scorie sono l'ossido di calcio (CaO sotto forma dicalce) e magnesio (MgO sotto forma di dolomite e magnesite.). Queste sostanze vengono caricate con rottami o soffiate nel forno durante la fusione.
Un altro componente importante è l'ossido di ferro, formato quando l'acciaio viene bruciato con l'introduzione di ossigeno. Successivamente, quando riscaldato, il carbonio (sotto forma di carbone) viene iniettato in questo strato, reagendo con l'ossido di ferro per formare metallo e monossido di carbonio. Ciò si traduce in schiumatura delle scorie, con conseguente maggiore efficienza termica. Il rivestimento previene i danni al tetto e alle pareti laterali del forno causati dal calore radiante.
Combustione delle impurità
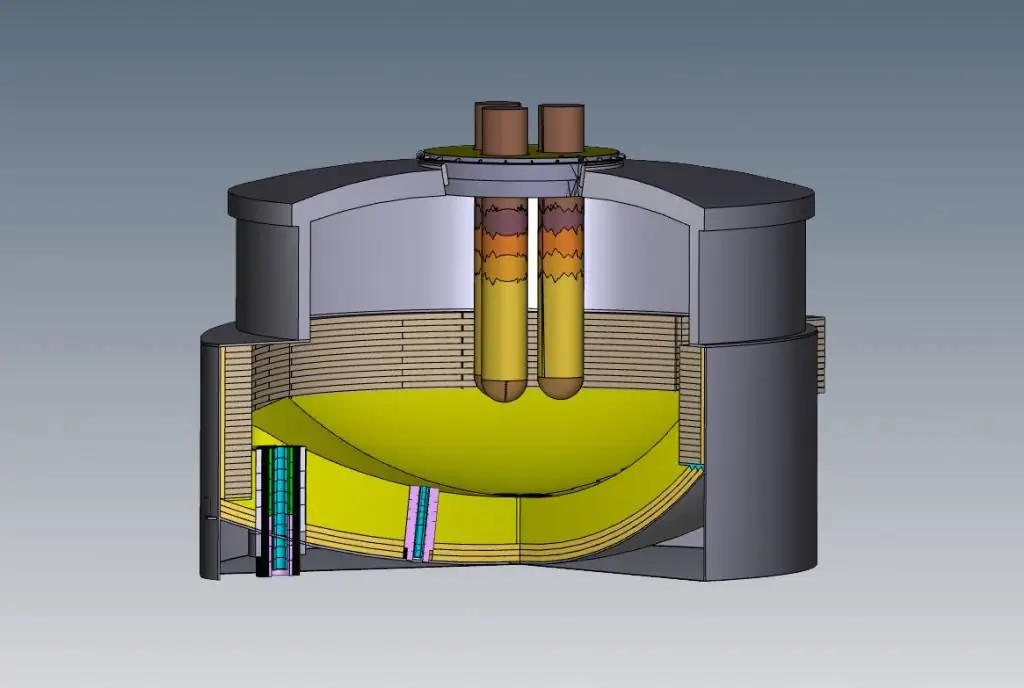
Una volta che i rottami metallici sono completamente fusi e viene raggiunta una vasca piatta, un altro secchio può essere caricato nel forno. Dopo che la seconda carica è completamente fusa, vengono eseguite operazioni di raffinazione per controllare e correggere la composizione chimica dell'acciaio e surriscaldare la massa fusa oltre il suo punto di congelamento in preparazione alla maschiatura. Vengono introdotti più formatori di scorie e molto ossigeno entra nel bagno, bruciando impurità come silicio, zolfo, fosforo, alluminio, manganese e calcio e rimuovendo i loro ossidi nelle scorie.
La rimozione del carbonio avviene dopo che questi elementi si sono esauriti per primi, poiché sono più simili all'ossigeno. I metalli che hanno un'affinità inferiore al ferro, come nichel e rame, non possono essere rimossi per ossidazione e devono essere controllati solo attraverso la chimica. Questa è, ad esempio, l'introduzione del ferro e della ghisa ridotti direttamente menzionati in precedenza.
Scorie schiumosepersiste in tutto e spesso trabocca il forno per traboccare dalla porta nella fossa prevista. La misurazione della temperatura e la selezione chimica vengono eseguite utilizzando lance automatiche. L'ossigeno e il carbonio possono essere misurati meccanicamente con speciali sonde immerse nell'acciaio.
Vantaggi di produzione
Utilizzando un sistema di controllo per forni ad arco per la fusione dell'acciaio, è possibile produrre acciaio dal 100% di materia prima - rottami metallici. Ciò riduce notevolmente l'energia richiesta per produrre la sostanza, rispetto alla produzione primaria dai minerali.
Un altro vantaggio è la flessibilità: mentre gli altiforni non possono variare in modo significativo e possono funzionare per anni, questo può essere avviato e spento rapidamente. Ciò consente all'acciaieria di variare la produzione in base alla domanda.
Il tipico forno per acciaio ad arco è la fonte di acciaio per il mini mulino, che può produrre prodotti in barre o nastri. I mini-smelter possono essere situati relativamente vicino ai mercati siderurgici e le esigenze di trasporto sono inferiori rispetto a un impianto integrato, che di solito si trova vicino alla costa per l'accesso alle spedizioni.
Dispositivo per forno ad arco in acciaio
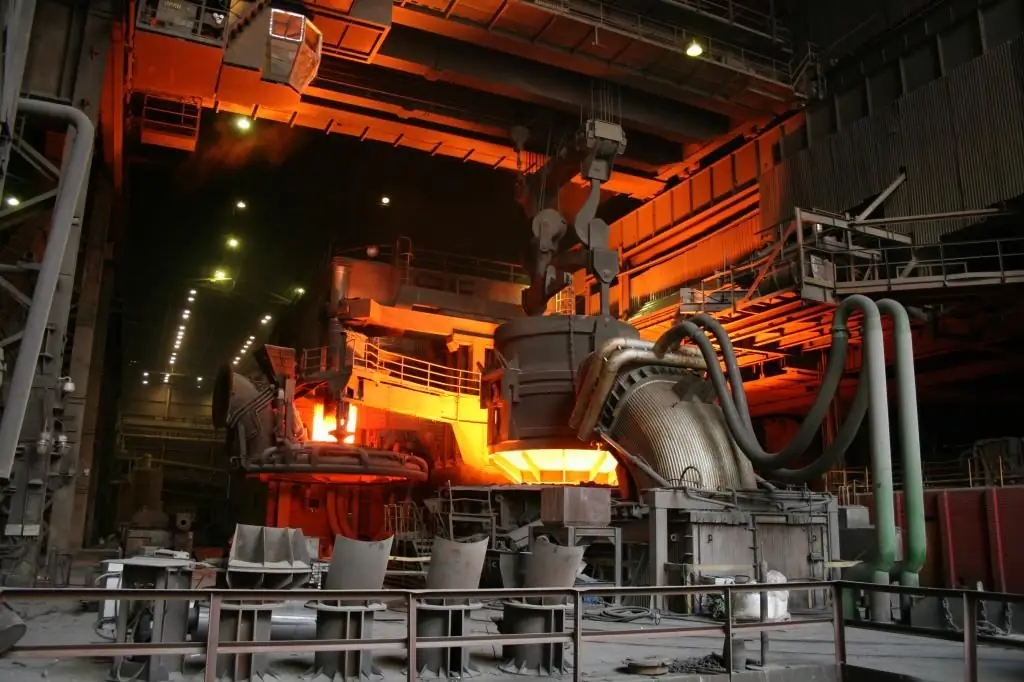
La sezione trasversale schematica è un elettrodo che viene sollevato e abbassato da una trasmissione a pignone e cremagliera. La superficie è rivestita con mattoni refrattari e rivestimento di fondo. La porta permette l'accesso all'internoparti del dispositivo. Il corpo del forno poggia sui bilancieri in modo che possa essere inclinato per la maschiatura.
Consigliato:
Acciaio inossidabile per alimenti: GOST. Come identificare l'acciaio inossidabile per uso alimentare? Qual è la differenza tra acciaio inossidabile alimentare e acciaio inossidabil

L'articolo parla dei gradi di acciaio inossidabile per uso alimentare. Leggi come distinguere l'acciaio inossidabile alimentare da quello tecnico
Alesatrice diamantata: tipologie, dispositivo, principio di funzionamento e condizioni di funzionamento
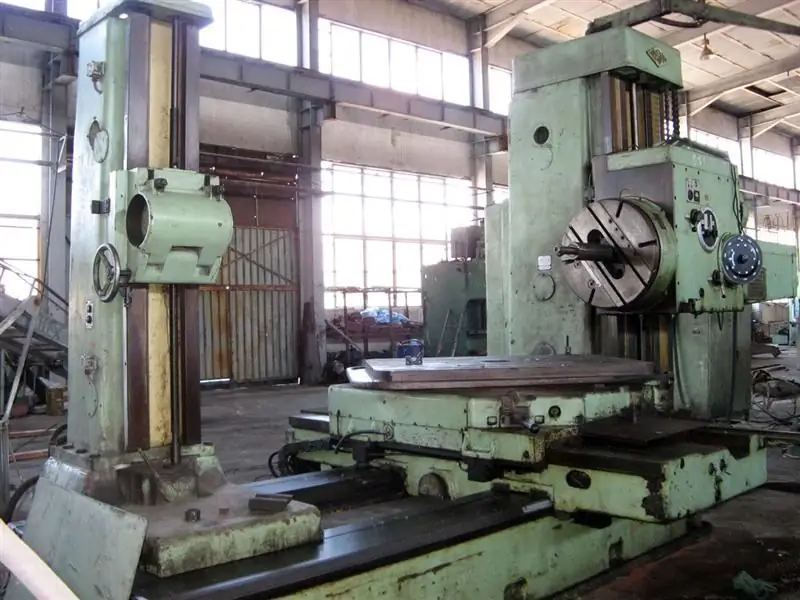
La combinazione di una configurazione complessa della direzione di taglio e di un'attrezzatura di lavoro a stato solido consente all'attrezzatura di alesatura diamantata di eseguire operazioni di lavorazione dei metalli estremamente delicate e critiche. Tali unità sono affidate alle operazioni di creazione di superfici sagomate, correzione di fori, ravvivatura di estremità, ecc. Allo stesso tempo, la foratrice diamantata è universale in termini di possibilità di applicazione in vari campi. Viene utilizzato non solo nelle industrie specializzate, ma anche nelle officine private
Cos'è la potenza reattiva? Compensazione della potenza reattiva. Calcolo della potenza reattiva
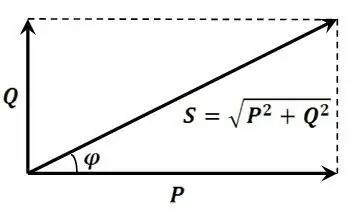
Nelle condizioni reali di produzione prevale la potenza reattiva di natura induttiva. Le imprese installano non un contatore elettrico, ma due, di cui uno attivo. E per la spesa eccessiva di energia "inseguita" invano attraverso le linee elettriche, le autorità competenti vengono multate senza pietà
Sensori di controllo della fiamma: caratteristiche, dispositivo e principio di funzionamento
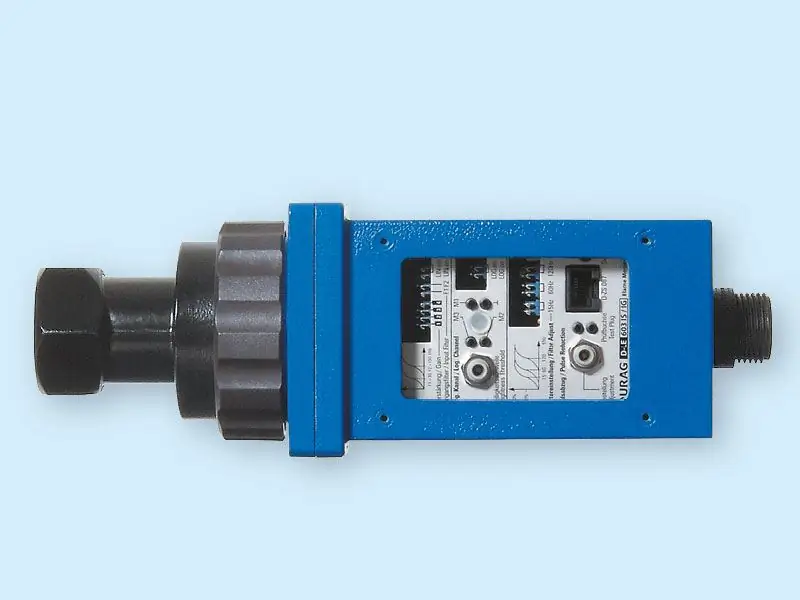
Oggi le persone usano attivamente il fuoco per i propri scopi. Tuttavia, è molto pericoloso e quindi, quando si lavora con esso, è necessario mettere la sicurezza al primo posto. Su scala industriale, questo ruolo è svolto da un sensore di controllo della fiamma
Laser a fibra di itterbio: dispositivo, principio di funzionamento, potenza, produzione, applicazione
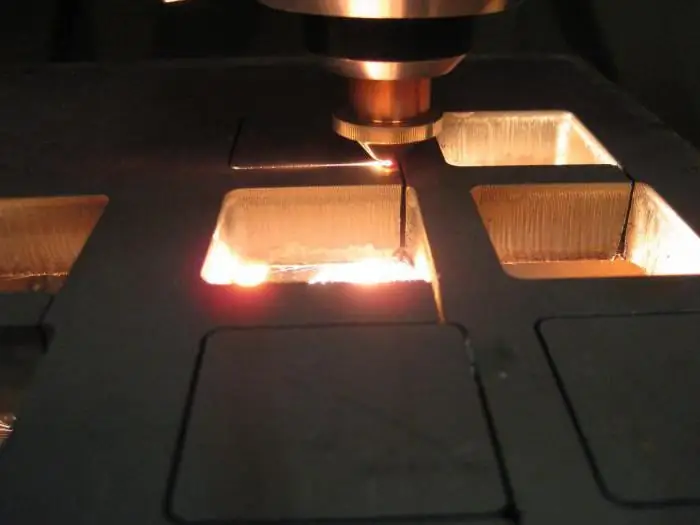
I laser a fibra sono compatti e robusti, puntano con precisione e dissipano facilmente l'energia termica. Si presentano in molte forme e, avendo molto in comune con altri tipi di generatori quantistici ottici, hanno i loro vantaggi unici