2025 Autore: Howard Calhoun | [email protected]. Ultima modifica: 2025-01-24 13:19
La colata in stampi a conchiglia è anche chiamata colata a conchiglia. E all'estero, questo metodo di lavoro si chiama Shell.
Informazioni generali
Nell'industria industriale di oggi vengono utilizzati molti metodi di colata diversi. Oltre alla colata in conchiglia, viene utilizzata anche la microfusione, nonché in stampi di metallo e molti altri metodi. Il vantaggio generale di questi metodi di colata, rispetto allo stampaggio in sabbia, è che si traducono in materiali finali più accurati in termini di forma e dimensioni. Inoltre, il numero di rugosità sulla superficie di tali prodotti è ridotto. In casi più rari, ma succede comunque che venga eliminata la necessità di lavorazioni successive dopo la fusione. Oltre a tutto, l'uso della colata in stampi a conchiglia e altri metodi contribuisce al fatto che questo processo può essere meccanizzato il più possibile, di conseguenza aumenta anche la sua automazione. E questo, ovviamente, aumenta notevolmente la produttività di qualsiasi struttura industriale.
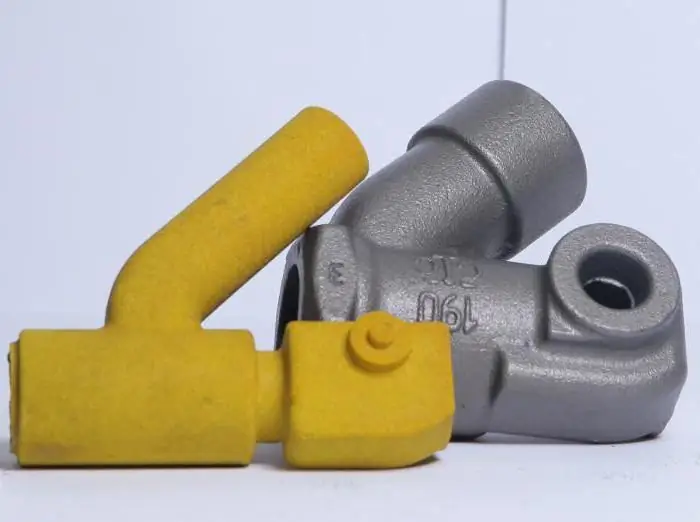
Fusione di conchiglie
Se parliamo specificamente di questometodo, è stato introdotto per la prima volta nelle fabbriche nel 1953. Attualmente, il metodo è ampiamente utilizzato. Ad esempio, è la fusione in stampi a conchiglia che produce la maggior parte delle parti per il trattore Kirovets. Tutte le parti prodotte con questo metodo sono di altissima qualità in acciaio o ghisa. La colata in conchiglia è un metodo in cui il risultato finale della colata ha una forma costituita da due gusci di sabbia-resina. Inoltre, questo metodo di produzione delle parti viene utilizzato solo nei casi in cui è necessario creare una parte di piccole o medie dimensioni, ma allo stesso tempo con un'elevata precisione. Esempi di applicazioni per questo metodo di colata sono parti di motori o getti a parete sottile.
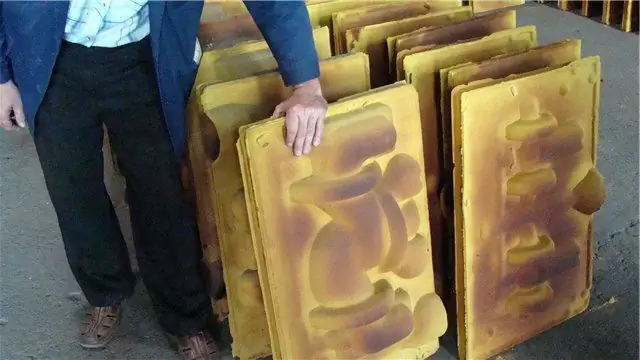
L'essenza della via
Con questo metodo di lavoro, puoi ottenere varie parti per ventilatori, motori, pompe o macchine tessili. Tuttavia, la lunghezza massima del prodotto ricevuto non può superare 1 metro e non può essere più pesante di 200 kg.
L'essenza della colata in stampi a conchiglia si basa su alcune proprietà delle resine termoindurenti, che fanno parte delle miscele sabbia-resina. Il vantaggio dell'utilizzo di tali componenti è che queste resine tendono a indurire rapidamente e in modo permanente se trattate con una temperatura di 200-250 gradi Celsius.
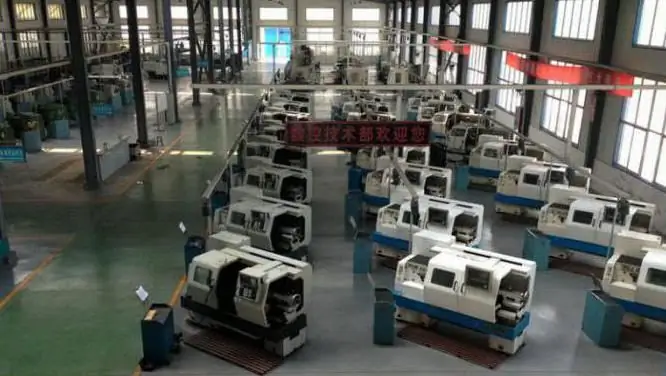
Creare uno stampo a conchiglia per la colata
Per realizzare uno stampo per la successiva colata, è necessario disporre di sabbia di quarzo a grana fine, che viene fornita con l'aggiunta di una resina termoindurente, che è il suo elemento di raccordo per ottenere uno stampo a conchiglia a tutti gli effetti. Questi materiali, in particolare la resina, sono scelti perché induriscono quando superano una certa barriera termica. Il processo di produzione è il seguente. Innanzitutto, la resina viene riscaldata a 140-160 gradi Celsius. Sotto l'influenza di un tale ambiente, si trasforma in una massa adesiva liquida che avvolge completamente lo stampo di sabbia di quarzo.
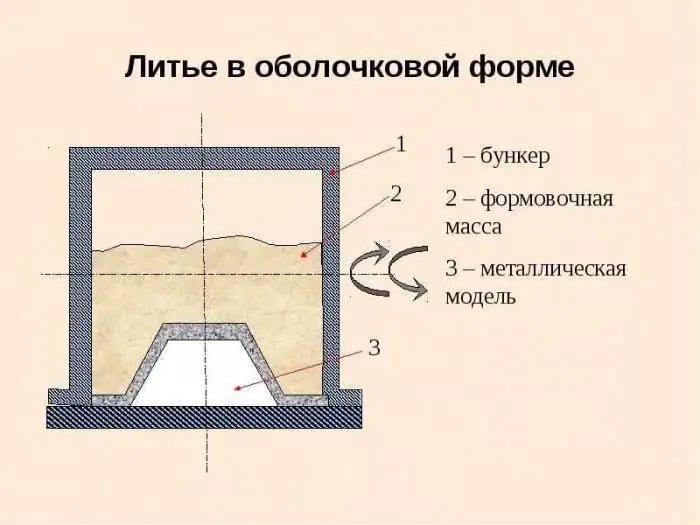
Lo scopo della colata in stampi a conchiglia è piuttosto ampio, e quindi il processo di realizzazione degli stampi viene portato in automatico o automatizzato.
Dopo che lo stampo è completamente ricoperto di resina, la temperatura viene aumentata a 200-250 gradi Celsius. Questa soglia di temperatura è sufficiente perché la massa adesiva si indurisca irreversibilmente e formi una forma. Inoltre, quando inizia il processo di fusione delle parti, cioè quando il metallo fuso entra nello stampo, la temperatura al suo interno raggiunge circa 600 gradi. Questa modalità è sufficiente per garantire che la resina non si sciolga, ma si bruci, lasciando dei pori sullo stampo stesso, facilitando la fuoriuscita dei gas.
Vantaggi e svantaggi della colata in conchiglia
Come qualsiasi altro processo di produzione, questo ha i suoi pro e contro. Se confrontiamo questo metodo di fusione, ad esempio, con la fusionenormali stampi in sabbia, ci sono diversi vantaggi:
- La prima e piuttosto significativa differenza è la classe di precisione, che è 7-9. Inoltre, la finitura superficiale della parte ottenuta viene migliorata fino a 3-6. Inoltre, vengono ridotte le tolleranze, che sono consentite per la lavorazione successiva della parte risultante dopo la fusione.
- Uno dei grandi vantaggi è una significativa riduzione dei costi di manodopera per la produzione di getti.
- Questo metodo di colata riduce il consumo di materiali di stampaggio, così come la quantità di metallo grazie al fatto che le dimensioni dei canali del cancello sono ridotte.
- Ridotto significativamente l'ammontare della produzione matrimoniale.
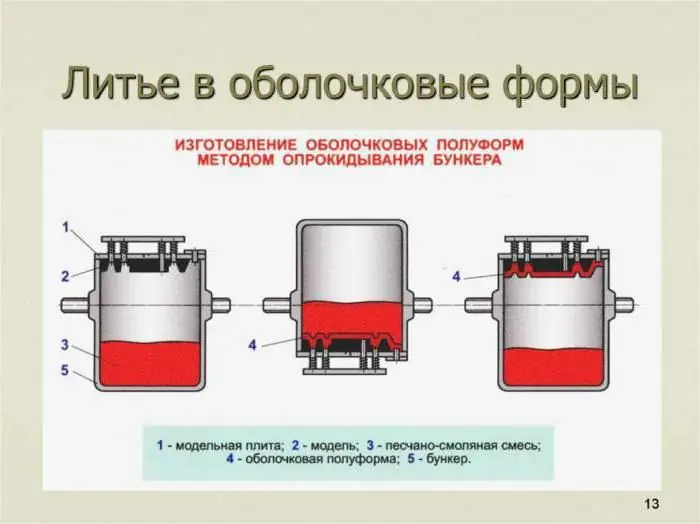
Tuttavia, ci sono alcuni svantaggi della fusione in stampi a conchiglia. Questi includono:
- Durata dello stampo a conchiglia - 1 colata.
- Il costo dello stampaggio della sabbia è piuttosto alto.
- Alta percentuale di gas nocivi.
Processo di formazione del corpo
Il processo di formazione del corpo si svolge in sei fasi:
- Il primo passo è il processo di versare la miscela su un modello di metallo caldo, così come il processo di conservarlo per diverse decine di secondi fino a quando non si forma una crosta sottile e forte attorno alla parte. Molto spesso, i modelli sono realizzati in ghisa e il loro riscaldamento viene effettuato fino a 230-315 gradi.
- Dopodiché, è necessario eseguire un'operazione di rimozione della sabbia di stampaggio in eccesso. Lo spessore della crosta dovrebbe eventualmente essere compreso tra 10 e 20mm. Dipende dal tempo di permanenza della miscela sul modello, oltre che dalla temperatura.
- Dopodiché, è necessario trasferire la piastra modello insieme allo stampo nel forno, dove rimarranno fino alla fine del processo di stagionatura. Al termine di questa procedura, la forza del guscio dovrebbe essere compresa tra 2,4 e 3,1 MPa.
- Dopo essere stato rimosso dal forno, il guscio indurito viene spostato dalla piastra. Per questa procedura viene utilizzato uno speciale pulsante.
- Successivamente, due o più modelli vengono fissati insieme utilizzando una sorta di morsetto o mediante incollaggio. Questi stampi possono essere utilizzati per la colata in stampi a conchiglia o semplicemente conservati. Scadenza quasi illimitata.
- Prima di iniziare il processo di colata nello stampo finito, vi viene versato un granello, che aiuta a prevenire o distruggere lo stampo durante l'ulteriore colata.
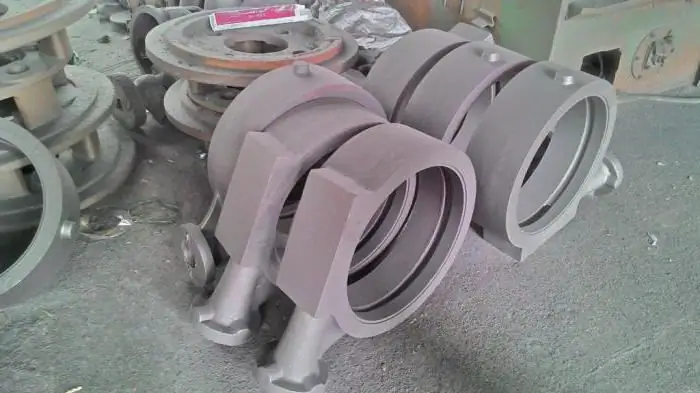
Dettagli sul casting
Vale la pena iniziare dal fatto che le tolleranze tipiche consentite nella produzione di utensili possono essere 0,5 mm. La rugosità superficiale è consentita nell'intervallo da 0,3 a 0,4 micron. Tali limiti sono giustificati dal fatto che viene utilizzata sabbia a grana fine. Da notare anche: l'uso della resina contribuisce notevolmente al fatto che la superficie è molto liscia.
Volumi di produzione
Per essere impegnati nella produzione di tali stampi e parti, è necessario occuparsi dell'installazione di un modello di stampo. Il tempo necessario per l'installazione è inferiore a una settimana. Al termine dell'installazione, la quantità di output puòraggiungere da 5 a 50 pezzi all'ora. Tali volumi di produzione all'ora sono abbastanza reali, tuttavia, per questo è necessario preparare di conseguenza il processo di colata. I principali materiali necessari per la fusione sono ghisa, alluminio, rame e leghe di questi tipi di metalli. Un altro materiale necessario sarà una lega che utilizzi alluminio e magnesio.
Consigliato:
Banca commerciale. Funzioni e operazioni di base
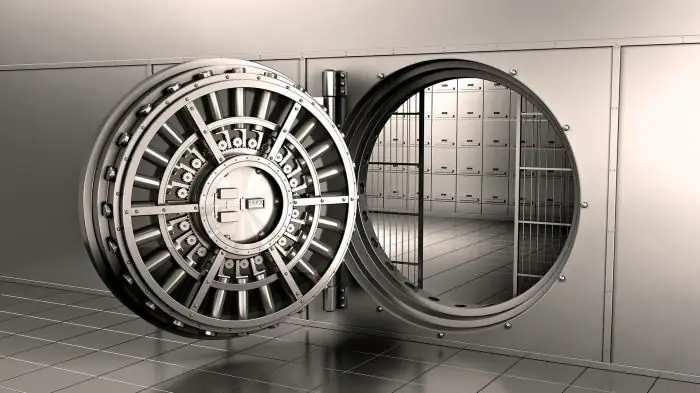
Un collegamento importante nel sistema bancario è una banca commerciale. Le funzioni e le operazioni principali di questa organizzazione sono finalizzate all'ottenimento del massimo profitto
Operazioni in contanti e credito delle banche. Tipi di operazioni bancarie
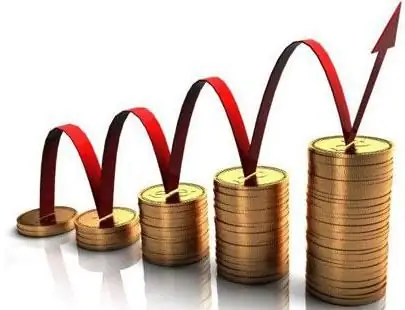
Le principali operazioni svolte da una banca commerciale sono credito e contanti. Quali sono le loro specifiche? Secondo quali regole vengono eseguite?
Fusione in stampo di silicone: attrezzatura. Colata sottovuoto in stampi di silicone
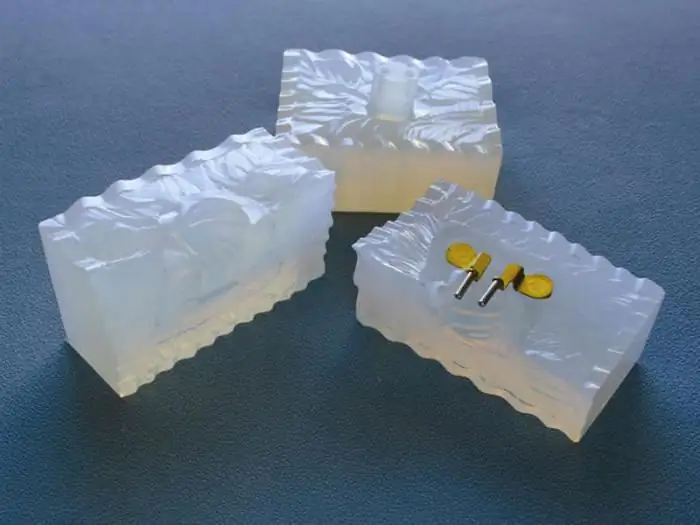
Per la produzione di un numero limitato di grezzi di plastica, viene spesso utilizzata la colata sottovuoto in stampi di silicone. Questo metodo è abbastanza economico (la realizzazione di uno stampo in metallo richiede più tempo e denaro). Inoltre, gli stampi in silicone vengono utilizzati ripetutamente e questo riduce anche notevolmente i costi di produzione
Tipi di operazioni bancarie. Servizi di liquidazione e cassa. Operazioni di banche con titoli
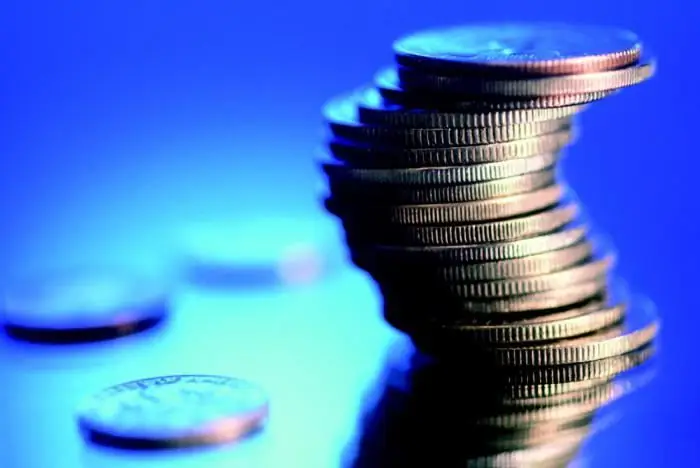
Prima di sapere quali tipi di transazioni bancarie esistono, devi comprendere alcune delle definizioni più importanti. Ad esempio, qual è l'istituzione in questione? Nella moderna terminologia economica, la banca agisce come un'unità finanziaria e di credito che esegue tutti i tipi di operazioni sia con denaro che con titoli
Per quanto tempo viene rilasciata una licenza per effettuare operazioni bancarie?

La decisione sulla registrazione statale di qualsiasi organizzazione finanziaria è presa dalla Banca centrale russa. Non appena le informazioni sulla banca entrano nel registro unificato, è obbligata a informare su tutte le modifiche in corso. Una licenza per le operazioni bancarie è rilasciata anche dalla Banca Centrale della Federazione Russa