2025 Autore: Howard Calhoun | [email protected]. Ultima modifica: 2025-01-24 13:19
L'uso di modelli di investimento è un metodo di produzione di fonderia abbastanza diffuso. Il metodo si distingue per la complessità del processo tecnologico e gli elevati costi di manodopera per i processi preparatori. Pertanto, viene utilizzato dove è necessario osservare accuratamente le dimensioni e garantire un'elevata qualità della superficie dei pezzi. È così che vengono fuse le pale delle turbine e gli strumenti ad alte prestazioni, le protesi dentarie e i gioielli, nonché le sculture di configurazione complessa. L'essenza della fusione a cera persa è che lo stampo per la colata è un pezzo unico, il modello di materiali a basso punto di fusione non viene rimosso durante lo stampaggio, ma viene fuso. Ciò garantisce un'attenta osservanza delle dimensioni e dei rilievi. Il metallo viene versato nella cavità rimanente dal modello. Al termine del raffreddamento, lo stampo viene distrutto e il prodotto viene rimosso. Quando si colano grandi serie, il costo del prodotto si riduce.
Vantaggi del metodo
Il vantaggio principale della microfusione è l'accuratezza del trasferimento dello stampo e la bassa rugosità superficiale. Inoltre, sono disponibili altri vantaggi:
- Disponibile la produzione di parti in lega leggermente lavorate.
- Riduce la necessità di ulteriori lavorazioni.
- I prodotti vengono fusi che altrimenti dovrebbero essere realizzati in parti e assemblati insieme.
- Con le grandi serie, si ottiene una riduzione dell'intensità di manodopera specifica (per un prodotto) e del relativo costo.
- Possibilità di meccanizzazione e parziale automazione delle operazioni preparatorie del getto stesso.
Questi vantaggi rendono il metodo uno dei più popolari e utilizzati nella metallurgia odierna, specialmente in combinazione con i moderni metodi di colata progressiva.
Svantaggi della microfusione
Gli indubbi vantaggi del metodo, a quanto pare, avrebbero dovuto assicurarne il predominio tra gli altri metodi. Tuttavia, nonostante la popolarità del metodo di microfusione, gli svantaggi ne hanno impedito l'adozione diffusa. Lo svantaggio principale è la complessità del processo a più stadi. Richiede attrezzature tecnologiche piuttosto complesse e costose per le fasi preparatorie. Per prodotti semplici prodotti in piccoli lotti, questo metodo ha un costo maggiore.
Per l'applicazione conveniente della colata a cera persa, vengono confrontati i vantaggi e gli svantaggi del metodo, la decisione sula sua scelta viene effettuata sulla base di una valutazione del rapporto qualità/prezzo. Viene quindi utilizzato principalmente per i prodotti più critici e costosi, difficilmente ottenibili in altro modo, come pale di turbine, sculture, utensili ad alta velocità, ecc. Altro campo di applicazione sono le fusioni su larga scala, in cui l'effetto scala consente di ottenere una significativa riduzione dei costi.
Tecnologia
La tecnologia di colata a cera persa è un processo di produzione a più stadi che richiede relativamente manodopera. Nella prima fase viene realizzato un modello master, che diventerà lo standard per la produzione di modelli funzionanti dopo aver attraversato tutte le fasi del prodotto finale. Per la produzione di un modello master vengono utilizzate sia composizioni di modelli speciali che tradizionali - gesso o legno. Il materiale del modello principale dovrebbe combinare resistenza e facilità di lavorazione.
Inoltre, la tecnologia di microfusione prevede la creazione di uno stampo in cui verranno colati tutti i modelli funzionanti. Gli stampi sono fatti di gesso, gomma, silicone, meno spesso metallo. Strutturalmente, deve essere necessariamente staccabile e predisposto per un uso ripetuto. Lo stampo viene riempito con una composizione del modello, dopo che si è indurito, viene smontato e il successivo modello funzionante viene rimosso.
Quando si producono parti uniche o piccole tirature, le fasi di creazione di un layout principale e di uno stampo vengono s altate e un layout (o più) viene realizzato modellando il materiale manualmente.
Il prossimo passo nel processo di microfusione èfabbricazione intorno al layout (o blocco di layout) dello stampo di colata. Queste matrici sono strutturalmente già inseparabili e monouso, il che consente di ottenere un'attenta osservanza delle dimensioni e della rugosità del prodotto. Nell'industria moderna vengono utilizzati due tipi di stampi - i tradizionali stampi in sabbia-argilla per la colata nel terreno e gli stampi a conchiglia - per la produzione di parti precise e costose.
Dopo che lo stampo è completato, il modello viene fuso da esso riscaldandolo o soffiando con vapore surriscaldato. Le forme a conchiglia vengono ulteriormente rafforzate riscaldando fino a 1000 ˚С.
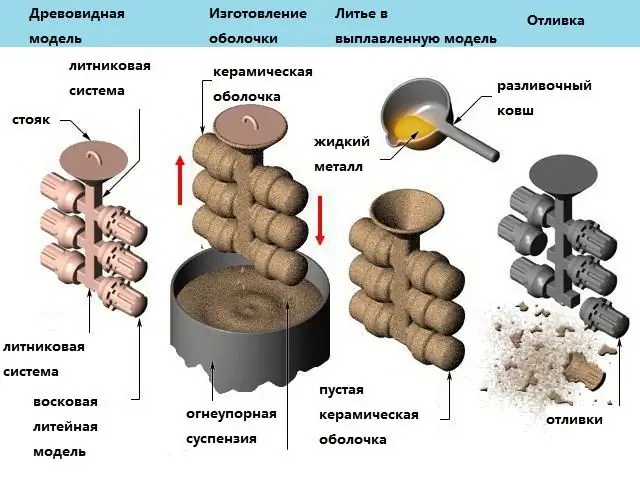
La fase finale del processo comprende la colata vera e propria del prodotto, il suo raffreddamento in condizioni naturali o con un metodo speciale in un termostato, la distruzione dello stampo e la pulizia del prodotto. Il metodo permette di ottenere getti di alta qualità che pesano da diversi grammi a decine di chilogrammi.
Formazioni di modelli
Il materiale per la produzione del layout deve avere determinate proprietà. Dovrebbe avere proprietà come:
- Plasticità in fase solida. È necessario ripetere accuratamente la forma del prodotto futuro e correggerlo se necessario.
- Forza. Il modello deve resistere senza deformarsi al processo di formazione di una forma attorno ad esso.
- Fusibile. Il rendering di un modello non dovrebbe richiedere molto tempo ed energia.
- Flessibilità fusa. La composizione dovrebbe penetrare facilmente in tutti i recessi e nei dettagli del rilievo, ripetendo esattamente i contorni del dettaglio futuro.
- Economia. Particolarmente importante per la produzione di grandi serie.
Per le composizioni del modello, viene solitamente utilizzata una miscela di stearina e paraffina. Questi materiali completano con successo i parametri dell' altro, compensando il punto di fusione insufficiente della paraffina e l'eccessiva viscosità della stearina.
Le composizioni a base di cera di lignite non sono meno popolari nel settore. Le sue proprietà principali sono la resistenza all'umidità, la forza e la capacità di formare rivestimenti molto lisci, particolarmente preziosi per la modellazione dei prodotti.
Si utilizzano anche composti costituiti da una miscela di cera di lignite, paraffina e stearina.
Creazione stampi
Per la produzione di prodotti unici, viene preparato un layout ritagliando un pezzo di materiale del modello manualmente o secondo modelli. Anche i modelli sotto forma di corpi di rivoluzione vengono realizzati al tornio. Recentemente, il metodo di stampa 3D dei modelli è diventato sempre più diffuso. È adatto sia per layout singoli che per piccole serie.
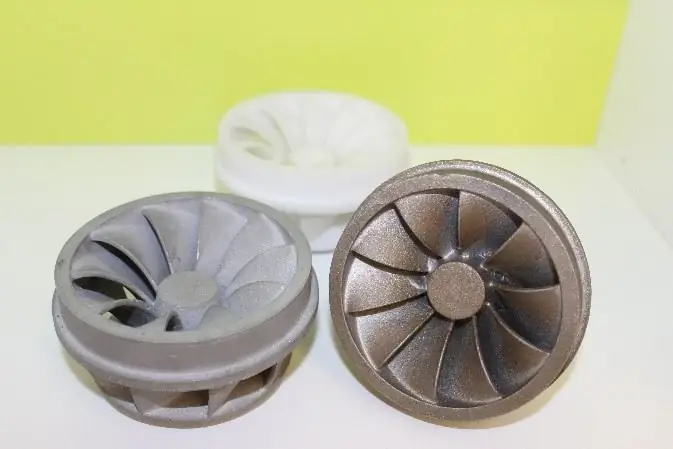
Il costo di una moderna stampante 3D industriale è ancora elevato, ma grazie alla facilità di riconfigurazione da un prodotto all' altro, può diventare un efficace strumento di modellistica in caso di un gran numero di ordini eterogenei di piccole serie.
Per realizzare un gran numero di layout identici, una matrice è fatta di gesso, gomma, silicone o metallo. I layout di lavoro vengono prodotti, a loro volta, mediante fusione in una matrice. In base alla progettazione, lo stampo deve essere pieghevole per garantire la possibilità di produrre un determinato numero di modelli. Il materiale selezionato dovrebbe anche fornire tale opportunità, pertanto gli vengono imposti requisiti come resistenza, densità, bassa rugosità e inerzia chimica in relazione al layout. La sostanza dello stampo deve anche avere un'adesione minima al modello per garantire che i modelli finiti possano essere facilmente rimossi e le dimensioni rispettate. Una proprietà importante dello stampo è la sua robustezza e resistenza all'usura, soprattutto per le grandi serie.
Creare modelli e blocchi
Un metodo ampiamente utilizzato per la produzione di modelli di rivestimento consiste nel fonderli a bassa pressione negli stampi. L'iniezione della miscela liquida avviene sia manualmente, mediante siringhe a pistone, sia con compressori meccanici, idraulici o pneumatici. Nel caso di utilizzo della cera di lignite, è necessario riscaldare le tubazioni per fornire la composizione a causa della sua elevata viscosità. I modelli in polistirene espanso sono realizzati per estrusione su presse automatizzate.
Per aumentare l'efficienza economica e ridurre l'intensità del lavoro in caso di produzione in serie di piccoli getti, i loro layout sono combinati in blocchi. I sistemi di iniezione sono formati sopra i blocchi collegando i singoli layout alle materozze utilizzando un saldatore manuale. Nel caso di fusioni singole o piccole serie i modelli sono realizzati a mano.
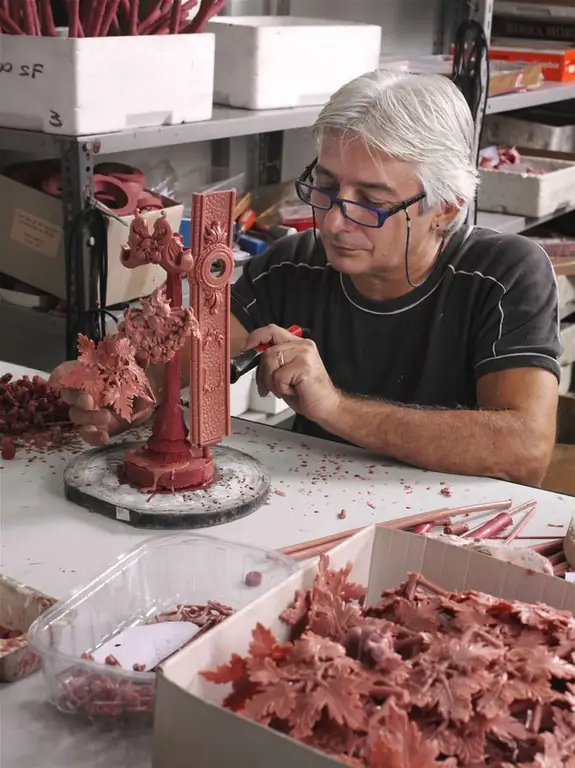
Quando si formano sistemi di gating, è necessario garantire un flusso non turbolento del fuso, un riempimento uniforme di tutti gli elementi della matrice. Quando si riempie un modulo da PGS, è inoltre necessario monitorare il riempimento uniforme di tuttiaperture tra le materozze e prevenzione dei danni.
Fare uno stampo
Nel metodo di microfusione in esame, ci sono due tipi principali di stampi:
- Miscele sabbia-argilla (SGM).
- Shell.
Gli stampi per colata a cera fluata vengono utilizzati principalmente nella produzione di piccole serie di prodotti che non richiedono una precisione molto elevata. Il processo di fabbricazione è piuttosto laborioso e richiede abilità elevate e spesso uniche di modellatori e modellatori. La meccanizzazione parziale si presta solo ad alcune operazioni, come la preparazione e riempimento della sabbia di formatura, la sua rincalzatura.
Gli stampi a conchiglia, invece, vengono utilizzati per produrre parti che richiedono una precisione di fabbricazione speciale. Il processo di fabbricazione è più complesso e lungo, ma si presta meglio alla meccanizzazione.
Fusione a terra
Questo è il primo metodo di lavorazione dei metalli padroneggiato dall'umanità. È stato dominato dai nostri antenati contemporaneamente all'inizio dell'uso di prodotti in metallo come armi, strumenti o utensili, cioè circa 5 mila anni fa. Il metallo fuso viene versato in una matrice preparata da una miscela di sabbia e argilla. I primi luoghi per la lavorazione dei metalli sorsero appena nelle vicinanze si trovavano depositi di metalli sotto forma di pepite e placer. Un tipico esempio è lo stabilimento di Kasli negli Urali, famoso in tutto il mondo per la sua fusione di pizzi di ferro.
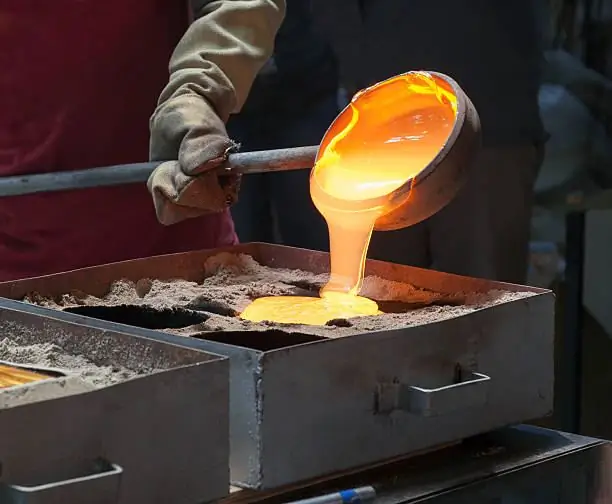
Il metodo della microfusione viene utilizzato per la fabbricazione di prodotti in metallo, sia ferrosi checolorato. E solo per i metalli che mostrano una maggiore tendenza a reagire in fase liquida (come il titanio), è necessario realizzare matrici da altre composizioni.
Il processo produttivo della colata in PGS si compone delle seguenti fasi:
- modellismo;
- preparare il pallone;
- riempimento e compattazione del composto nel pallone;
- fusione di metallo;
- rimozione e pulizia del getto.
Modulo da ASG - monouso. Per ottenere il prodotto finito, dovrà essere rotto. Allo stesso tempo, la maggior parte della miscela è disponibile per il riutilizzo.
Composizioni di prevalentemente sabbie di quarzo di varie granulometrie e argille plastiche, il cui contenuto varia dal 3 al 45 percento, sono utilizzate come materiali per ASG. Quindi, ad esempio, i getti artistici vengono prodotti utilizzando una miscela con un contenuto di argilla del 10-20%, per getti particolarmente grandi, il contenuto di argilla viene regolato al 25%.
Sono utilizzati due sottotipi:
- Miscele di rivestimento. Si trovano sulla superficie interna dello stampo e interagiscono con il metallo fuso. Devono essere resistenti al calore, in grado di non essere distrutti dalle differenze di temperatura e dalle sollecitazioni che ne derivano. Queste miscele hanno una grana fine per trasmettere con cura i dettagli della superficie. Anche la capacità della miscela di far passare il gas è molto significativa.
- Miscele di ripieno. Sono utilizzati per il riempimento tra lo strato di rivestimento e le pareti del pallone. Devono resistere al peso del metallo colato, mantenere la forma del prodotto e contribuire alla rimozione tempestiva e completa dei gas. Prodotto da tipi di sabbia più economici,riutilizzabile.
Se i gas di colata non fuoriescono attraverso le masse della sabbia di formatura, ma attraverso il sistema di iniezione, si verificano difetti nella colata, che portano al matrimonio.
La tradizionale tecnologia di colata nel terreno è illustrata in dettaglio nel film di A. Tarkovsky "Andrei Rublev". Nel racconto "La campana", il giovane Boriska, figlio di un maestro defunto, dirige un'artel di fonderia e fonde una campana di chiesa.
Fusione di conchiglie
Il metodo della microfusione in stampi a conchiglia è caratterizzato dal miglior trasferimento delle dimensioni del prodotto e dalla bassa rugosità superficiale. Il modello è realizzato con composti fusibili, come la cera di lignite. Anche le fonderie utilizzano ampiamente la composizione di paraffina-stearina in proporzioni uguali. Nel caso di getti di grandi dimensioni, i sali sono inclusi nel materiale del modello per proteggere il modello dalla deformazione. Immergendosi nella soluzione, il modello viene ricoperto in 6-10 strati con una sospensione ad alta temperatura.
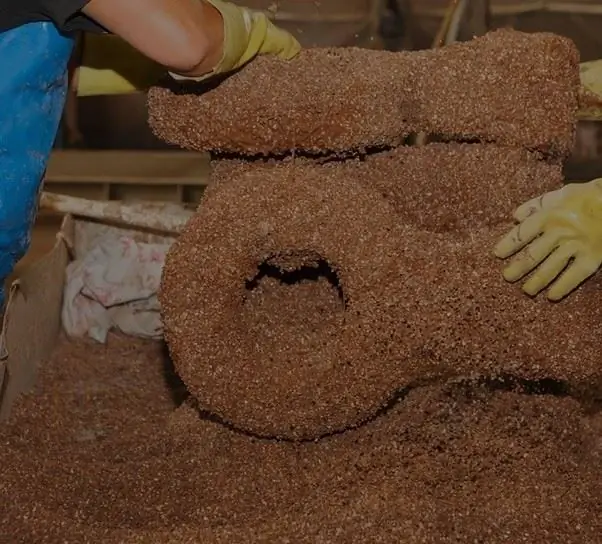
I silicati idrolizzati fungono da legante, l'elettrocorindone oi cristalli di quarzo vengono presi come spruzzatura resistente al calore. I materiali a conchiglia sono caratterizzati da elevata resistenza, bassa igroscopicità ed eccellente permeabilità ai gas.
Il layout viene essiccato in un'atmosfera di ammoniaca gassosa. Nella fase successiva, lo stampo viene riscaldato a 120 ˚C per rimuovere il modello in paraffina. I resti della miscela vengono rimossi con vapore surriscaldato ad alta pressione. Successivamente, lo stampo viene calcinato a temperature fino a 1000 ˚С, il che porta alla sua fissazione finale e rimozione delle sostanze,che possono essere rilasciati come gas durante il processo di colata.
Il guscio è posto in una specie di fiaschetta, che è ricoperta di pallini d'acciaio. Ciò aiuta a mantenere la configurazione durante il riempimento dello stampo con fuso e allo stesso tempo migliora le condizioni per il raffreddamento del getto. Il fuso viene versato in stampi riscaldati a 1000 ˚С. Dopo aver raffreddato il prodotto secondo un programma speciale in un termostato, lo stampo viene distrutto, la colata viene rimossa e pulita.
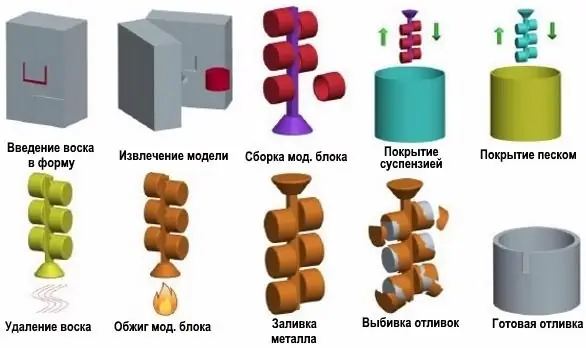
Il vantaggio principale di questo metodo di colata è l'elevata precisione dimensionale e la bassa rugosità superficiale.
Ulteriori vantaggi del metodo:
- Parti fuse da leghe difficili da lavorare.
- Lanciare oggetti che altrimenti dovrebbero essere lanciati a pezzi e poi rimontati.
Gli svantaggi di questo metodo di colata a cera persa sono un basso utilizzo del metallo e una maggiore intensità di manodopera.
Fusione di precisione
Colata a cera persa di precisione: questo è il nome dato sia alla tecnologia che al prodotto finale stesso. L'elevata precisione della colata è assicurata dal fatto che durante la preparazione dello stampo non è necessario estrarre da esso il modello del prodotto. Quando si utilizza il metodo tradizionale, la produzione di una matrice di colata è un processo multifase complesso e che richiede molto tempo. Ciò è particolarmente vero nel caso di getti di parti di configurazione complessa, con rientranze, depressioni e cavità interne.
Ad esempio, quando si fonde un vaso in ghisa o rame con una curvatura superficiale variabile, è necessario utilizzare molti trucchi. Sì, primala metà inferiore della fiaschetta viene imbottita, quindi il modello viene rimosso, capovolto e la metà superiore viene speronata. Il modello deve essere composto, le anse del vaso sono costituite da due elementi, vengono estratte attraverso la cavità del modello in due fasi: prima l'elemento inferiore, poi quello superiore. Tutte queste numerose torniture e trascinamenti non possono avere un effetto positivo sull'integrità della superficie dello stampo e, in definitiva, sull'accuratezza nel mantenimento delle dimensioni del getto e sulla qualità della sua superficie. Inoltre, rimane il problema di far combaciare accuratamente le parti dei flaconi e di fissarli saldamente l'uno all' altro.
La produzione di microfusione è priva di queste carenze, non richiede modellatori così altamente qualificati e riduce significativamente l'intensità del lavoro delle operazioni di prefabbricazione. Ciò è particolarmente pronunciato con grandi serie di getti.
Il metodo consente di raggiungere la 2-5a classe di precisione secondo GOST 26645-85. Ciò rende possibile la fusione di prodotti di alta precisione come pale di turbine, utensili da taglio, comprese frese e trapani ad alte prestazioni, staffe critiche per carichi elevati, piccole parti di veicoli ad alto carico, macchine utensili e altri meccanismi complessi.
L'elevata precisione dimensionale e l'elevata classe di superficie riducono al minimo la necessità di ulteriore lavorazione della fusione, risparmiando metallo e riducendo i costi di produzione.
Attrezzature
L'attrezzatura per la microfusione richiesta è varia e complessa. Le imprese li combinano in un unico e ben coordinato complesso,organizzato come sito, officina o produzione separata.
La composizione del complesso dipende dalla scala di produzione, dimensione, configurazione e circolazione dei getti.
Quindi, nella produzione di protesi dentarie e gioielli, l'attrezzatura includerà:
- tabella modello;
- forno a muffola con termostato;
- un set di bisturi e spatole per correggere la forma del modello;
- scheda di formazione;
- flask;
- serbatoi per lo stoccaggio e la preparazione della sabbia da stampaggio;
- set di strumenti costipatore per sabbia;
- crogiolo per la fusione del metallo;
- pinze;
- martello per rompere gli schemi.
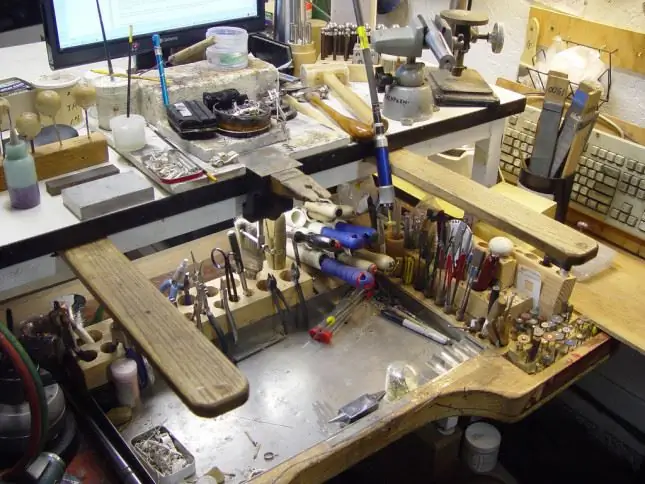
Questo complesso di produzione può facilmente stare su un tavolo e in un armadio. Se si prevede di produrre in serie, ad esempio, getti di alluminio - parti di un dispositivo, sarà necessaria l'attrezzatura per:
- modellare e colare stampi in ceramica;
- forme di essiccazione;
- fondere il materiale del modello e applicare uno strato resistente al calore;
- pulire i getti dal materiale di stampaggio.
E, infine, l'attrezzatura vera e propria del complesso di fonderia, progettata per ottenere un fuso e versarlo in uno stampo. Può essere un'attrezzatura per il casting:
- a bassa pressione;
- centrifugo;
- nel solito modo di gravità.
Le macchine per lo stampaggio a iniezione e la colata centrifuga sono separate altamente meccanizzate e automatizzatecomplesso produttivo, isolato dall'atmosfera del negozio. Riducono al minimo il lavoro manuale e l'esposizione umana a condizioni dannose. Le camere sigillate in cui si trovano i complessi forniscono una cattura e una purificazione complete dei gas di scarico, il che aumenta significativamente il rispetto dell'ambiente dell'impresa.
La fusione a cera persa ha un potenziale di sviluppo abbastanza elevato, specialmente se combinata con tecniche avanzate di realizzazione di stampi e colata.
Consigliato:
La fusione dell'acciaio: tecnologia, metodi, materie prime
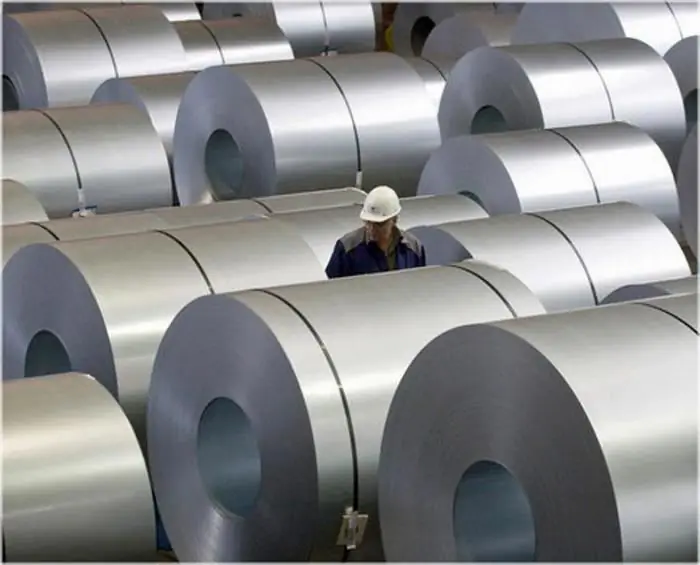
Il minerale di ferro si ottiene nel modo consueto: estrazione a cielo aperto o sotterranea e successivo trasporto per la preparazione iniziale, dove il materiale viene frantumato, lavato e lavorato
Incisione su plexiglas: vantaggi e svantaggi, tecnologia, attrezzature
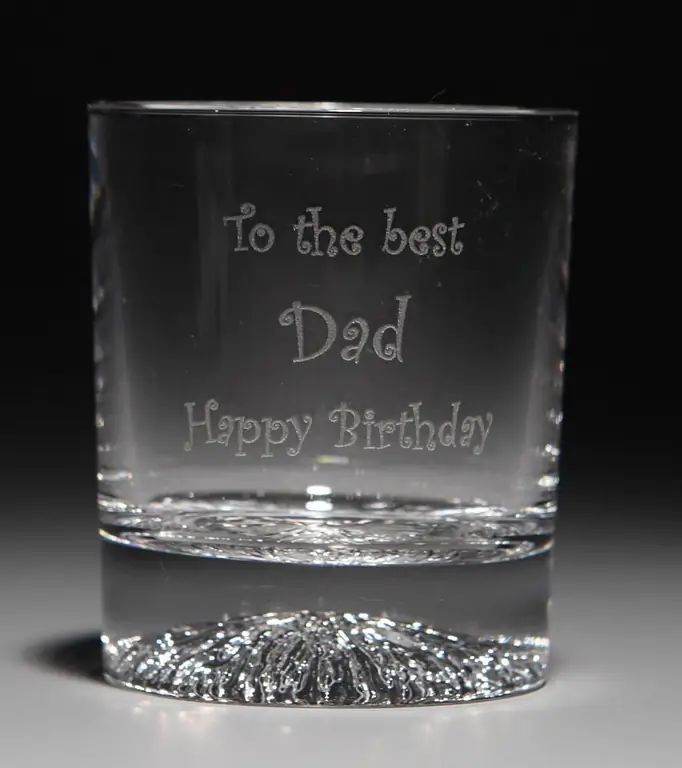
L'incisione su plexiglas è considerata un mestiere di pittura. Una statuetta ricordo, vetrate o un tavolo di vetro, decorati con squisiti disegni, incarnano un delicato gusto artistico. Le tecnologie di decapaggio e sabbiatura sono nel passato. Oggi, con l'aiuto di una macchina laser, ogni persona può creare uno schema altamente dettagliato
Letterpress è Tecnologia di stampa tipografica, moderne fasi di sviluppo, attrezzature necessarie, vantaggi e svantaggi di questo tipo di stampa
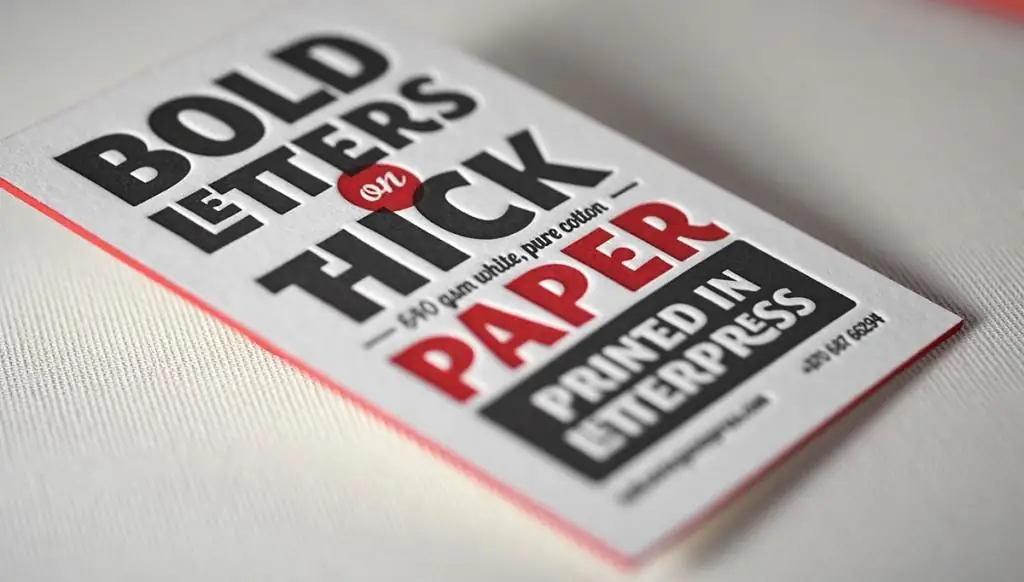
La stampa tipografica è uno dei metodi tipici per applicare le informazioni utilizzando una matrice in rilievo. Gli elementi che sporgono vengono ricoperti di vernice sotto forma di pasta e quindi premuti contro la carta. Così, vengono replicati vari periodici di massa, libri di consultazione, libri e giornali
Elaborazione ad ultrasuoni: tecnologia, vantaggi e svantaggi
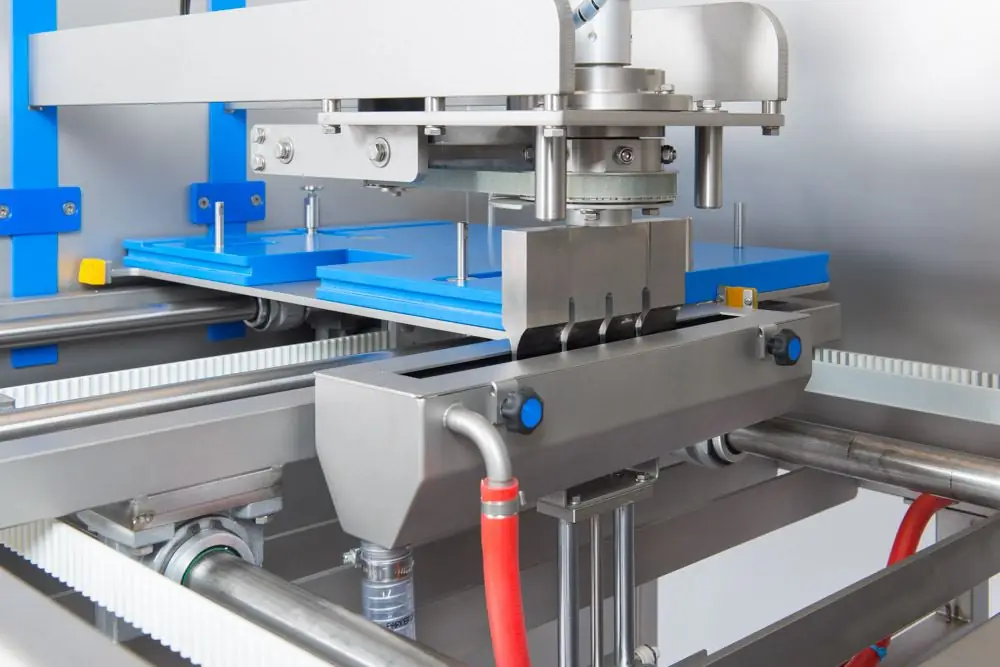
L'industria della lavorazione dei metalli in questa fase di sviluppo è in grado di risolvere i complessi compiti di taglio e foratura di pezzi di vari gradi di durezza. Ciò è diventato possibile grazie allo sviluppo di modi fondamentalmente nuovi di influenzare il materiale, incluso un ampio gruppo di metodi elettromeccanici. Una delle tecnologie più efficaci di questo tipo è il trattamento ad ultrasuoni (UZO), basato sui principi della radiazione elettroacustica
Tecnologia di fusione del ferro
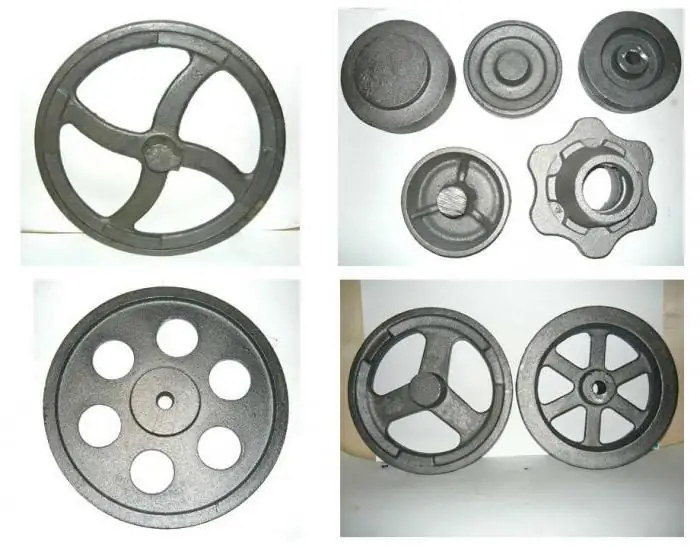
Una breve rassegna e descrizione della tecnologia dei prodotti in ghisa. Metodi, metodi e applicazioni delle parti in ghisa