2025 Autore: Howard Calhoun | [email protected]. Ultima modifica: 2025-01-24 13:18
Il minerale di ferro si ottiene nel modo consueto: estrazione a cielo aperto o sotterranea e successivo trasporto per la preparazione iniziale, dove il materiale viene frantumato, lavato e lavorato.
Il minerale viene versato in un altoforno e soffiato con aria calda e calore, che lo trasforma in ferro fuso. Viene quindi rimosso dal fondo del forno in stampi noti come maiali, dove viene raffreddato per produrre ghisa. Viene trasformato in ferro battuto o trasformato in acciaio in diversi modi.
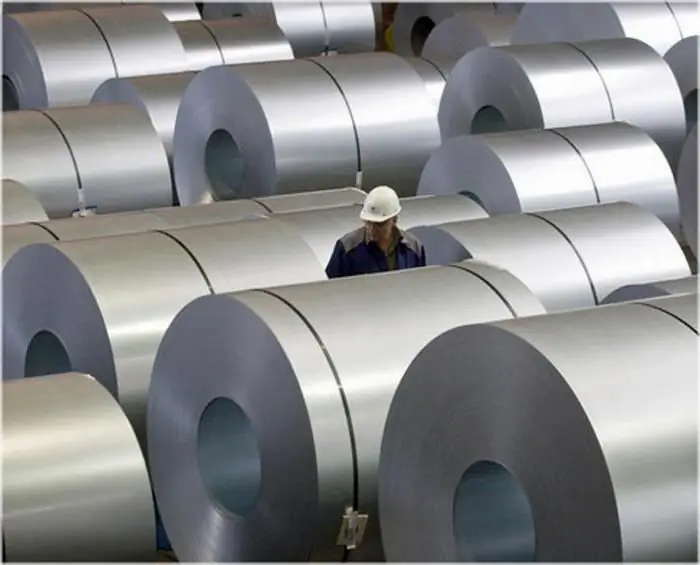
Cos'è l'acciaio?
All'inizio c'era il ferro. È uno dei metalli più comuni nella crosta terrestre. Può essere trovato quasi ovunque, in combinazione con molti altri elementi, sotto forma di minerale. In Europa la lavorazione del ferro risale al 1700 aC
Nel 1786, gli scienziati francesi Berthollet, Monge e Vandermonde determinarono accuratamente che la differenza tra ferro, ghisa e acciaio è dovuta al diverso contenuto di carbonio. Tuttavia, l'acciaio, fatto di ferro, divenne rapidamente il metallo più importante della rivoluzione industriale. All'inizio del 20° secolo la produzione mondiale di acciaio era di 28milioni di tonnellate - questo è sei volte di più rispetto al 1880. All'inizio della prima guerra mondiale, la sua produzione era di 85 milioni di tonnellate. Per diversi decenni ha praticamente sostituito il ferro.
Il contenuto di carbonio influisce sulle caratteristiche del metallo. Esistono due tipi principali di acciaio: legato e non legato. La lega di acciaio si riferisce a elementi chimici diversi dal carbonio aggiunti al ferro. Pertanto, per creare l'acciaio inossidabile viene utilizzata una lega con il 17% di cromo e l'8% di nichel.
Attualmente sono più di 3000 i marchi catalogati (composizioni chimiche), senza contare quelli creati per soddisfare le singole esigenze. Tutti contribuiscono a fare dell'acciaio il materiale più adatto alle sfide del futuro.
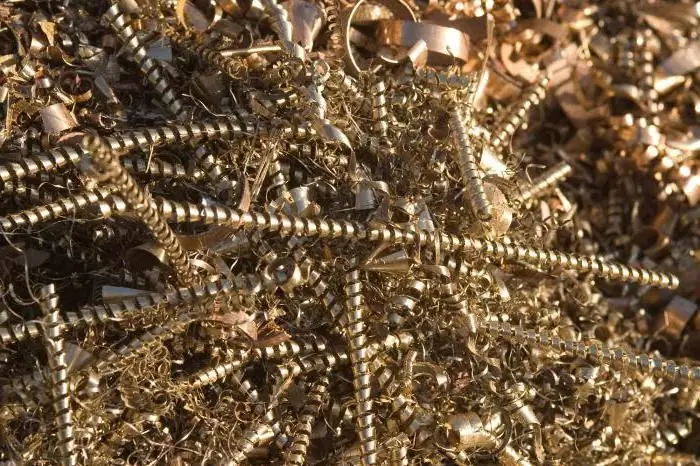
Materie prime siderurgiche: primarie e secondarie
Fondere questo metallo utilizzando molti componenti è il metodo di estrazione più comune. I materiali di carica possono essere sia primari che secondari. La composizione principale della carica, di regola, è il 55% di ghisa e il 45% dei restanti rottami metallici. Come elemento principale della lega vengono utilizzate ferroleghe, ghisa convertita e metalli commercialmente puri, di norma tutti i tipi di metalli ferrosi sono classificati come secondari.
Il minerale di ferro è la materia prima più importante e di base nell'industria siderurgica. Occorrono circa 1,5 tonnellate di questo materiale per produrre una tonnellata di ghisa. Per produrre una tonnellata di ghisa vengono utilizzate circa 450 tonnellate di coke. Molte ferrieresi usa anche la carbonella.
L'acqua è una materia prima importante per l'industria siderurgica. Viene utilizzato principalmente per l'estinzione del coke, il raffreddamento dell' altoforno, la produzione di vapore della porta della fornace a carbone, il funzionamento di apparecchiature idrauliche e lo sm altimento delle acque reflue. Occorrono circa 4 tonnellate di aria per produrre una tonnellata di acciaio. Il flusso viene utilizzato nell' altoforno per estrarre i contaminanti dal minerale di fonderia. Calcare e dolomite si combinano con le impurità estratte per formare scorie.
Sia gli altiforni che quelli in acciaio rivestiti di refrattari. Sono utilizzati per forni di rivestimento destinati alla fusione del minerale di ferro. Per lo stampaggio viene utilizzato biossido di silicio o sabbia. I metalli non ferrosi vengono utilizzati per produrre acciai di vari gradi: alluminio, cromo, cob alto, rame, piombo, manganese, molibdeno, nichel, stagno, tungsteno, zinco, vanadio, ecc. Tra tutte queste ferroleghe, il manganese è ampiamente utilizzato nella produzione dell'acciaio.
I rifiuti di ferro provenienti da strutture di fabbrica smantellate, macchinari, vecchi veicoli, ecc. vengono riciclati e ampiamente utilizzati nell'industria.
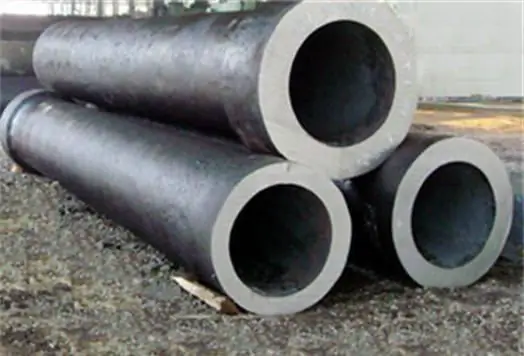
Ferro per acciaio
La fusione dell'acciaio con la ghisa è molto più comune che con altri materiali. Ghisa è un termine che di solito si riferisce alla ghisa grigia, tuttavia viene anche identificata con un ampio gruppo di ferroleghe. Il carbonio costituisce circa dal 2,1 al 4% in peso mentre il silicio è tipicamente dall'1 al 3% in peso nella lega.
La fusione del ferro e dell'acciaio avviene a temperaturapunto di fusione compreso tra 1150 e 1200 gradi, che è di circa 300 gradi inferiore al punto di fusione del ferro puro. La ghisa mostra anche una buona fluidità, un'eccellente lavorabilità, resistenza alla deformazione, all'ossidazione e alla colata.
L'acciaio è anche una lega di ferro con un contenuto di carbonio variabile. Il contenuto di carbonio dell'acciaio è compreso tra lo 0,2 e il 2,1% in massa ed è il materiale di lega più economico per il ferro. La fusione dell'acciaio dalla ghisa è utile per una varietà di scopi ingegneristici e strutturali.
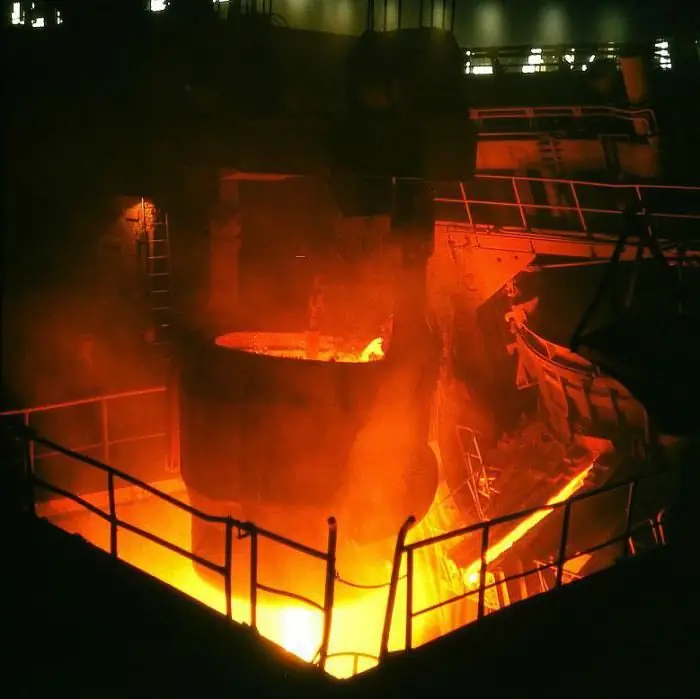
Minerale di ferro per acciaio
Il processo di produzione dell'acciaio inizia con la lavorazione del minerale di ferro. La roccia contenente minerale di ferro viene frantumata. Il minerale viene estratto utilizzando rulli magnetici. Il minerale di ferro a grana fine viene trasformato in grumi a grana grossa per l'uso in un altoforno. Il carbone viene raffinato in una cokeria per produrre una forma quasi pura di carbonio. La miscela di minerale di ferro e carbone viene quindi riscaldata per produrre ferro fuso, o ghisa, da cui viene prodotto l'acciaio.
Nella fornace principale ad ossigeno, il minerale di ferro fuso è la principale materia prima e viene miscelato con varie quantità di rottami di acciaio e leghe per produrre vari gradi di acciaio. In un forno elettrico ad arco, i rottami di acciaio riciclati vengono fusi direttamente in acciaio nuovo. Circa il 12% dell'acciaio è costituito da materiale riciclato.
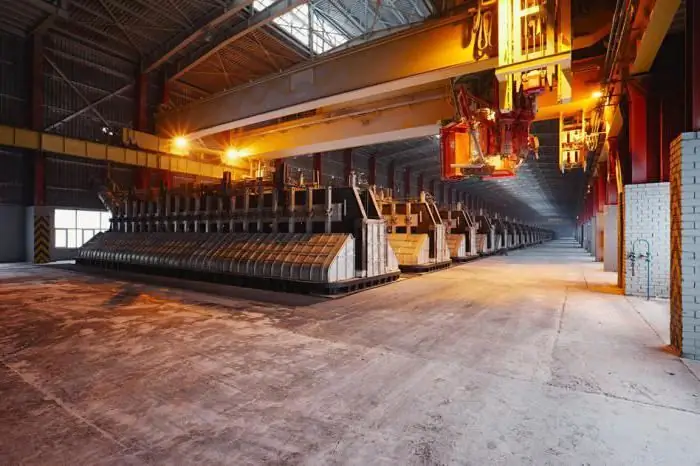
Tecnologia di fusione
La fusione è un processo mediante il quale si ottiene un metallo sotto forma di elemento,sia come composto semplice dal suo minerale riscaldando al di sopra del suo punto di fusione, solitamente in presenza di agenti ossidanti come l'aria o agenti riducenti come il coke.
Nella tecnologia di produzione dell'acciaio, il metallo combinato con l'ossigeno, come l'ossido di ferro, viene riscaldato a una temperatura elevata e l'ossido si forma in combinazione con il carbonio nel carburante, che viene rilasciato come monossido di carbonio o carbonio diossido. Altre impurità, chiamate collettivamente vene, vengono rimosse aggiungendo un flusso con il quale si combinano per formare scorie.
La moderna produzione di acciaio utilizza un forno a riverbero. Il minerale concentrato e il flusso (solitamente calcare) vengono caricati nella parte superiore, mentre il mascherino fuso (composto di rame, ferro, zolfo e scorie) viene prelevato dal basso. Un secondo trattamento termico in un forno di conversione è necessario per rimuovere il ferro dalla finitura opaca.
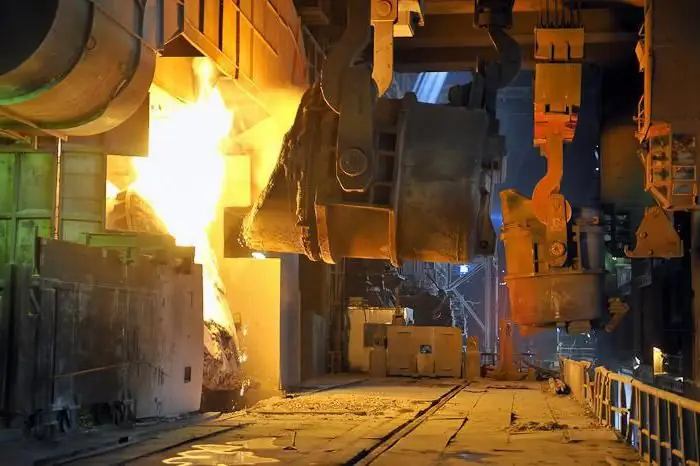
Metodo convettore di ossigeno
Il processo BOF è il processo di produzione dell'acciaio leader nel mondo. La produzione mondiale di acciaio per convertitori nel 2003 è stata di 964,8 milioni di tonnellate, pari al 63,3% della produzione totale. La produzione di convertitori è una fonte di inquinamento ambientale. I problemi principali di questo sono la riduzione delle emissioni, degli scarichi e la riduzione dei rifiuti. La loro essenza sta nell'uso dell'energia secondaria e delle risorse materiali.
Il calore esotermico è generato dalle reazioni di ossidazione durante lo spurgo.
Il principale processo di produzione dell'acciaio utilizzando il nostroscorte:
- Il ferro fuso (a volte chiamato metallo caldo) da un altoforno viene versato in un grande contenitore rivestito di refrattario chiamato mestolo.
- Il metallo nella siviera viene inviato direttamente alla fase principale di produzione dell'acciaio o di pretrattamento.
- L'ossigeno ad alta purezza a una pressione di 700-1000 kilopascal viene iniettato a velocità supersonica sulla superficie del bagno di ferro attraverso una lancia raffreddata ad acqua sospesa in un recipiente e tenuta a pochi metri sopra il bagno.
La decisione sul pretrattamento dipende dalla qualità del metallo caldo e dalla qualità dell'acciaio finale desiderata. I primissimi convertitori inferiori rimovibili che possono essere staccati e riparati sono ancora in uso. Le lance usate per soffiare sono state cambiate. Per evitare l'inceppamento della lancia durante il soffiaggio, sono stati utilizzati collari scanalati con una lunga punta rastremata in rame. Le punte della punta, dopo la combustione, bruciano la CO formata quando soffiata in CO2 e forniscono calore aggiuntivo. Freccette, palline refrattarie e rilevatori di scorie vengono utilizzati per rimuovere le scorie.
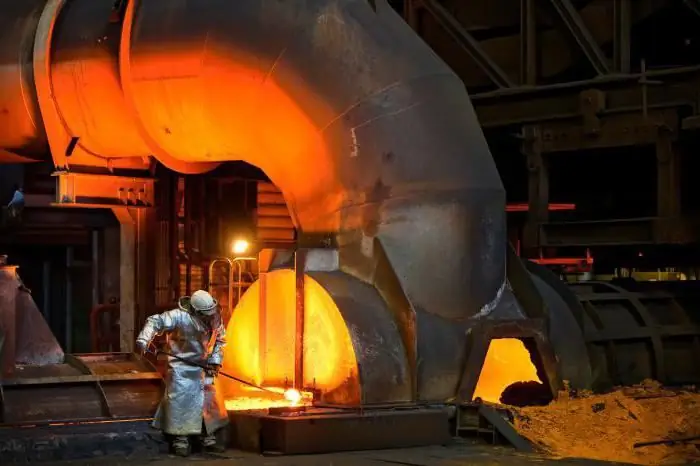
Metodo convettore ossigeno: vantaggi e svantaggi
Non richiede il costo delle apparecchiature per la purificazione dei gas, poiché la formazione di polvere, ovvero l'evaporazione del ferro, si riduce di 3 volte. A causa della diminuzione della resa del ferro, si osserva un aumento della resa dell'acciaio liquido dell'1,5 - 2,5%. Il vantaggio è che l'intensità del soffiaggio in questo metodo aumenta, il che dàla capacità di aumentare le prestazioni del convertitore del 18%. La qualità dell'acciaio è maggiore perché la temperatura nella zona di spurgo è più bassa, il che si traduce in una minore formazione di azoto.
Le carenze di questo metodo di fusione dell'acciaio hanno portato a una diminuzione della domanda di consumo, poiché il livello di consumo di ossigeno aumenta del 7% a causa dell'elevato consumo di combustione del carburante. C'è un maggiore contenuto di idrogeno nel metallo riciclato, motivo per cui ci vuole del tempo dopo la fine del processo per effettuare uno spurgo con ossigeno. Tra tutti i metodi, il convertitore di ossigeno ha la più alta formazione di scorie, il motivo è l'impossibilità di monitorare il processo di ossidazione all'interno dell'apparecchiatura.
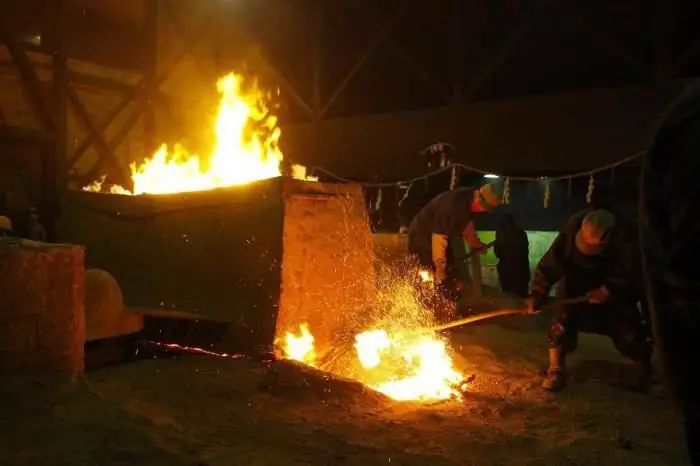
Metodo a cuore aperto
Il processo a focolare aperto per la maggior parte del 20° secolo è stata la parte principale della lavorazione di tutto l'acciaio prodotto nel mondo. William Siemens, negli anni '60 dell'Ottocento, cercò un mezzo per aumentare la temperatura in una fornace metallurgica, resuscitando una vecchia proposta di utilizzare il calore di scarto generato dalla fornace. Riscaldò il mattone ad alta temperatura, quindi usò lo stesso percorso per introdurre l'aria nel forno. L'aria preriscaldata ha aumentato notevolmente la temperatura della fiamma.
Come combustibile vengono utilizzati gas naturale o oli pesanti atomizzati; aria e carburante vengono riscaldati prima della combustione. Il forno viene caricato con ghisa liquida e rottami di acciaio insieme a minerale di ferro, calcare, dolomite e fondenti.
La stufa stessa è fatta dimateriali altamente refrattari come i mattoni del focolare in magnesite. I forni a suola aperta pesano fino a 600 tonnellate e sono generalmente installati in gruppi, in modo che le massicce apparecchiature ausiliarie necessarie per caricare i forni e lavorare l'acciaio liquido possano essere utilizzate efficacemente.
Sebbene il processo a focolare aperto sia stato quasi completamente sostituito nella maggior parte dei paesi industrializzati dal processo a ossigeno di base e dal forno elettrico ad arco, produce circa 1/6 di tutto l'acciaio prodotto nel mondo.
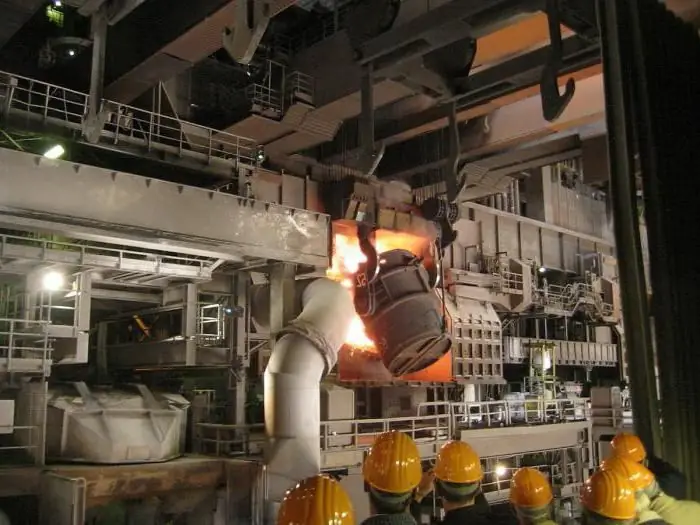
Vantaggi e svantaggi di questo metodo
I vantaggi includono la facilità d'uso e la facilità di produzione dell'acciaio legato con vari additivi che conferiscono al materiale varie proprietà specializzate. Gli additivi e le leghe necessari vengono aggiunti immediatamente prima della fine della fusione.
Gli svantaggi includono un'efficienza ridotta rispetto al metodo del convertitore di ossigeno. Inoltre, la qualità dell'acciaio è inferiore rispetto ad altri metodi di fusione dei metalli.
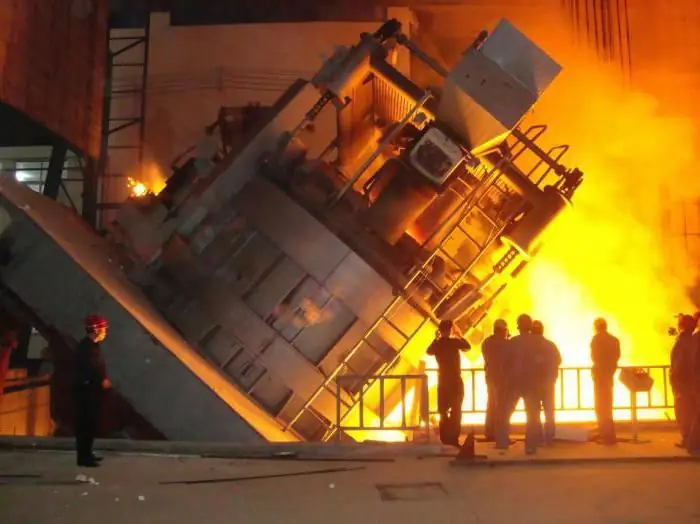
Metodo di fabbricazione dell'acciaio elettrico
Il metodo moderno per fondere l'acciaio utilizzando le nostre riserve è un forno che riscalda un materiale carico con un arco elettrico. I forni industriali ad arco hanno dimensioni variabili da piccole unità con una capacità di circa una tonnellata (utilizzate nelle fonderie per la produzione di prodotti siderurgici) a unità da 400 tonnellate utilizzate nella metallurgia secondaria.
Forni ad arco,utilizzato nei laboratori di ricerca può avere una capacità di poche decine di grammi. Le temperature dei forni elettrici ad arco industriali possono raggiungere fino a 1800 °C (3.272 °F), mentre le installazioni di laboratorio possono superare i 3000 °C (5432 °F).
I forni ad arco differiscono dai forni a induzione in quanto il materiale di carica è direttamente esposto a un arco elettrico e la corrente nei terminali passa attraverso il materiale caricato. Il forno elettrico ad arco viene utilizzato per la produzione dell'acciaio, è costituito da un rivestimento in refrattario, generalmente raffreddato ad acqua, di grandi dimensioni, coperto da un tetto a scomparsa.
Il forno è diviso principalmente in tre sezioni:
- Guscio costituito da pareti laterali e vasca inferiore in acciaio.
- Il focolare è costituito da un refrattario che estrae la vasca inferiore.
- Il tetto rivestito in refrattario o raffreddato ad acqua può essere realizzato a sezione sferica oa tronco di cono (sezione conica).
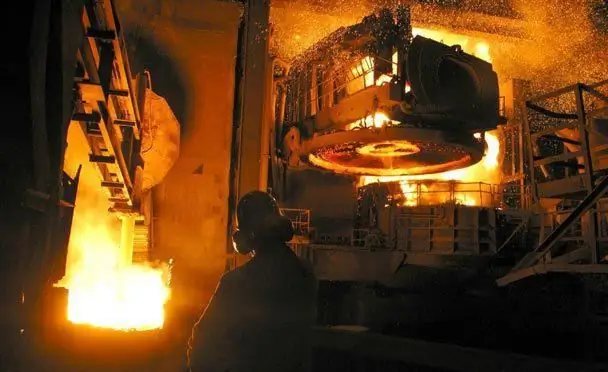
Vantaggi e svantaggi del metodo
Questo metodo occupa una posizione di primo piano nel campo della produzione di acciaio. Il metodo di fusione dell'acciaio viene utilizzato per creare metallo di alta qualità che è completamente privo o contiene una piccola quantità di impurità indesiderate come zolfo, fosforo e ossigeno.
Il principale vantaggio del metodo è l'uso dell'elettricità per il riscaldamento, quindi puoi controllare facilmente la temperatura di fusione e ottenere un'incredibile velocità di riscaldamento del metallo. Il lavoro automatizzato diventeràuna piacevole aggiunta all'eccellente opportunità per la lavorazione di alta qualità di vari rottami metallici.
Gli svantaggi includono un elevato consumo energetico.
Consigliato:
Acciaio inossidabile per alimenti: GOST. Come identificare l'acciaio inossidabile per uso alimentare? Qual è la differenza tra acciaio inossidabile alimentare e acciaio inossidabil

L'articolo parla dei gradi di acciaio inossidabile per uso alimentare. Leggi come distinguere l'acciaio inossidabile alimentare da quello tecnico
L'industria dell'abbigliamento come branca dell'industria leggera. Tecnologie, attrezzature e materie prime per l'industria dell'abbigliamento
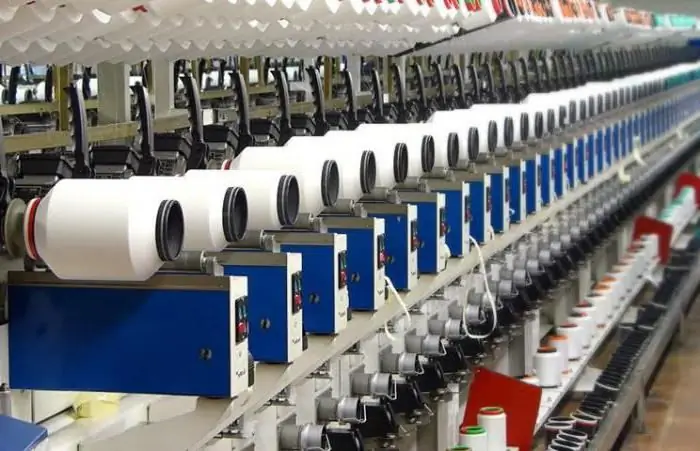
L'articolo è dedicato all'industria dell'abbigliamento. Vengono considerate le tecnologie utilizzate in questo settore, attrezzature, materie prime, ecc
Ottenere alcoli: metodi e materie prime
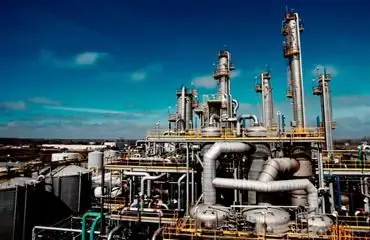
L'ottenimento di alcol è un processo tecnologico piuttosto complicato. Esistono metodi biochimici e chimici per ottenere alcoli. L'ottenimento di alcol metilico viene effettuato attraverso l'uso di varie tecnologie
Qual è la nomenclatura delle materie prime dell'attività economica estera?
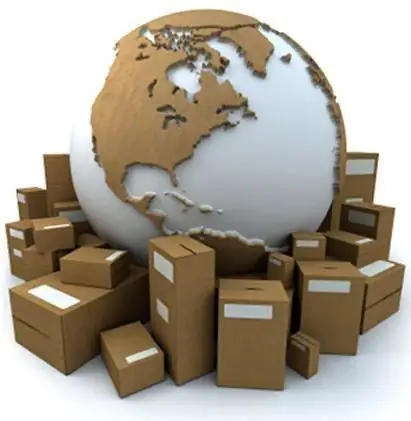
Ogni unità di prodotto sdoganata è sottoposta a uno speciale processo di identificazione. Di conseguenza, riceve il codice della nomenclatura delle merci dell'attività economica estera
Scienza delle materie prime: metodi di scopi e obiettivi
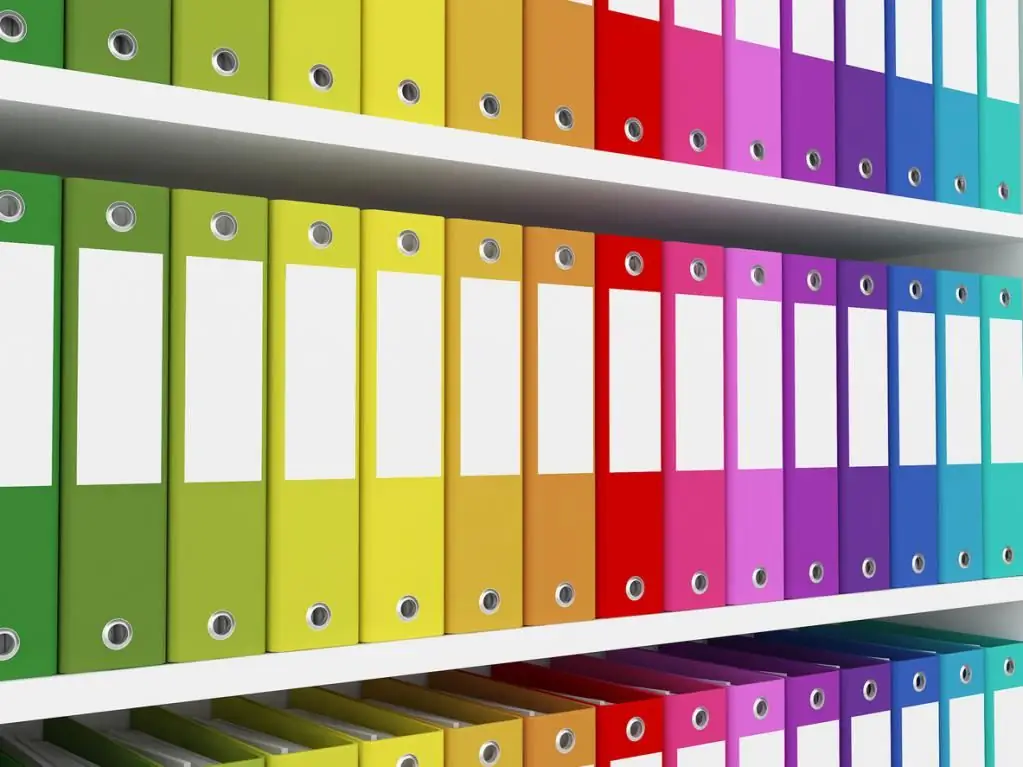
Grazie ai moderni metodi di ricerca sulle materie prime, i suoi compiti principali sono risolti. I metodi di ricerca sulle merci aiutano a cercare modi per migliorare la qualità delle merci, condurre un esame, scegliere le modalità ottimali di funzionamento, imballaggio e trasporto. In altre parole, per fare tutto ciò che richiede la scienza delle merci come scienza e strumento economico